Our expert article “Standstill? No, thanks” can be found in WIRE magazine, issue 1/2022.
Expert article: Standstill? No, thanks
Two years of pandemic are behind the German industry and the forming sector and brought many changes. For some companies, this meant taking extraordinary measures to keep their businesses running, generate or process enough order volume and thus secure jobs.
Networked companies clearly at an advantage
In a recent survey by McKinsey, 94% of the 400 companies surveyed confirmed that they were able to continue or even increase their business and activities without restrictions thanks to their production, which was already efficiently networked before Corona. IT and MES expert Harald Kimmerle confirms: “Our numerous customers from the wire and metal industry were able to face the changed conditions more efficiently and adapt more quickly to the respective situation. They were and are clearly at an advantage.”
2022: Let’s do it
In the “Leitfaden Industrie 4.0”, the VDMA confirms on the basis of its study that the economy around the German mechanical engineering industry could record an increase in orders of 21% by the end of 2021 compared to the previous year. An upward trend that will continue in 2022.
But basically it is not decisive in which condition the market is. What is more important is the ability to adapt smoothly and react quickly to current market events, customers and changing requirements at any time. Gaining efficiency is and remains the top priority.
Intelligent networking as a problem solver
Today’s manufacturing challenges have a strong impact on productivity. The automotive industry, for example, continues to struggle with chip shortages. Entire production chains and lines are at a standstill or agreed call-off quantities vary widely. The supply chain problem also needs to be addressed. Price increases for raw materials, wire and strip, cannot be passed on and long delivery times not only delay the company’s own production, but also have a negative impact on customers. With flexible and transparent production, such challenges and problems are a thing of the past.
Maximum productivity through optimum networking
Controlling manufacturing in such a way that companies work more productively is the goal of iT Engineering Manufacturing Solutions GmbH, MES market leader in the metal forming industry. Managing Director Harald Kimmerle explains: “The basis is always the measurable recording and documentation of all resources of the different departments. Realistic and transparent planning is crucial. Common ERP systems only plan production roughly and assume an infinite production capacity. Our MES system, on the other hand, ensures resource-optimized machine assignment, visualizes order progress and calculates the end of the order.”
Every employee knows at any time what the disruptive factors are, for example, and what time sequences are shifted as a result, which machines need to be serviced or how many products still need to be manufactured in the current shift.
Next generation tool maintenance
One of the greatest challenges in manufacturing is keeping the machines running and thus avoiding production delays. And what applies to machines also applies to the various tools used. 50% of all machine downtimes have organizational reasons. “And we make that measurable,” says Harald Kimmerle.
The innovative MES system from iT Engineering Manufacturing Solutions GmbH records all relevant production data from the machines, the Internet of Things (IoT), the tools, the material and the components. It networks all departments of manufacturing, from planning and control to toolmaking, machine occupancy and the current order progress on the machine with each other in real time.
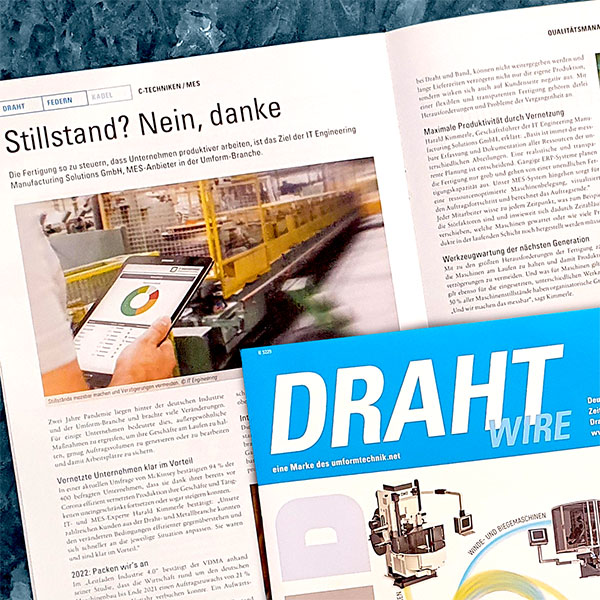