And how can all machines, no matter how old, be seamlessly integrated into the existing network?
Many companies that want to digitalize their production and thus make it future-proof are wondering how this works with their older existing machines. While newer machines already have a data interface (usually with Industry 4.0 standard OPC/UA) and can therefore be easily connected to the digital factory, older machines in particular do not have a suitable data interface.
In this case, data is recorded via 24V signals. For this purpose, IoT gateways are used as hardware for data acquisition, which reliably record the machine data. Another option is the use of PLC controllers or LAN adapters. This allows machines to be networked quickly and easily without an Ethernet CP and without changing the hardware and software configuration.
Both methods enable a seamless flow of information between machines and devices from different manufacturers and of any age.
The most important benefits and advantages of data acquisition from older machines without a data interface are
- Use of existing infrastructure
- Cost savings, as no expensive upgrades are necessary
- Simple integration into the digital system structure
- Less interference, even over longer cable runs
- No impairment of machine safety
- Fast implementation
Reliably record machine data
Machine data includes the number of parts, machine statuses, reasons for malfunctions, performance and process data such as temperatures, pressures or energy consumption.
The machine data acquisition of the MES Software EMC automatically records the number of units and quantities produced in real time. This replaces time-consuming, inaccurate and error-prone manual data entry. The machine data is visualized directly at the machine via an MES terminal.
Acquisition of data from all machines and peripherals with connectivity solution
With newer machines, machine data is recorded via the OPC/UA interface. With older machines, data is recorded via the existing 24V signals. These signals can be easily tapped without having to intervene deeply in the machine control system. Typical data recorded from 24V signals are, for example
- Machine on/off
- Fault on/off
- Cycle completed
- Cycle counter
- Aggregate states
In addition, data from peripherals such as tool monitoring, reels or test devices are also recorded in the EMC Machine Data Acquisition.
Seamless integration into the IT network
The devices and machines are simply integrated into the network, via cable or WLAN, without any additional IT infrastructure. This saves time and costs and enables efficient data collection.
The data collected from the machines is compatible with the existing ERP system and directly networked. The reliable networking and provision of data from machines with a connection to the ERP and network architecture enables a continuous improvement process and a reliable, always up-to-date overview of all machine statuses, downtime reasons and key figures such as OEE.
An exemplary data acquisition architecture could look like this:
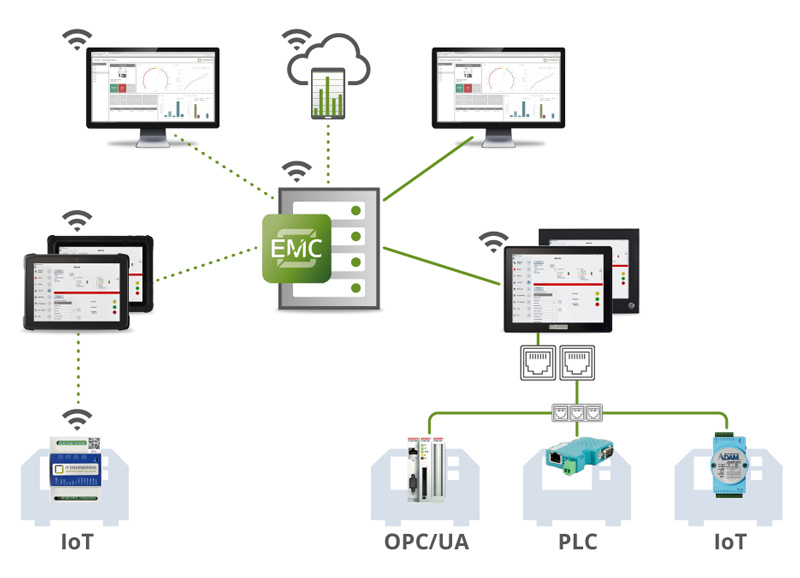
Perfectly record conditions and machine data and immediately identify reasons for downtime
The EMC Machine Data Acquisition module reliably and automatically records data from all machines in real time. In addition to the status of the machines, the MDA also records error information, necessary operator interventions and the status of maintenance. System malfunctions as well as production and downtimes can be detected immediately. In addition, reasons for faults can be easily stored at the actual time at the touch of a button.
This ensures modern and data-based production management. All production processes can be fully tracked at any time. The data obtained from machine data acquisition forms the basis for condition monitoring, noise time measurement, OEE recording, etc. They make it possible to quickly and easily derive measures to optimize production.
Conclusion
Even without a data interface, older machines can be digitized quickly and easily without having to intervene in the control logic. By tapping into existing 24V signals and using IoT gateways, operating states, cycles and downtimes can be reliably recorded and made available in real time. This allows companies to easily integrate their older existing machines digitally without having to invest in expensive new machines, thus creating the basis for transparency, OEE analyses and data-driven process optimization.
This is a motivating opportunity, especially for companies that want to future-proof their production: older machines are not an obstacle to networked production, but can become part of the digital value chain through simple retrofits. In this way, companies can make their smart factory a reality step by step and secure competitive advantages by gaining valuable data from existing systems in order to sustainably increase efficiency and availability.
Contact us
Do you have further questions about integrating your machines and their data acquisition with our MES Software EMC or about implementing your digital factory?
We will be happy to advise you and provide you with a personalized offer.
Simply call us on +49 7127 – 9231 10 or send us an e-mail to info@ite-ms.de
Frequently asked questions about data acquisition on older machines
How can older machines without a data interface be integrated into digital production?
Older machines can be recorded using retrofit solutions such as IoT modules. These make it possible to digitally record running times, downtimes and production quantities and transfer them to your MES system.
What are the advantages of retrofitting data acquisition on existing machines?
Companies gain transparency about capacity utilization and downtimes, can optimize maintenance cycles and obtain a solid basis for increasing efficiency without having to invest directly in new machines.
Which technologies are used for retrofitting?
For example, IoT gateways are used, which are installed directly in the machine cabinet to record relevant data via 24V signals and transmit it to your evaluation systems via WLAN or cable.
How time-consuming is it to retrofit older machines?
The effort involved is comparatively low, as no extensive conversions are required. The IoT devices can often be installed within a few hours and integration into existing systems is straightforward.
Can previously recorded machine data be subsequently integrated into an MES?
Yes, the previously recorded data (e.g. machine data, process data, production data acquisition) can be fed directly into your MES system afterwards in order to visualize production processes and enable the evaluation of OEE key figures and downtimes.