Our latest expert article ” Manufacturing today: digital and efficient”.
can now be found in the wire issue 2/2022 of WIRE magazine,
or here:
Manufacturing today: digital and efficient
In times of crises and wars, companies must constantly adapt to new challenges and respond digitally and efficiently. To date, some have hardly taken advantage of the opportunities offered by smart networked manufacturing with data-based analyses and digitized production processes in order to better safeguard themselves and optimally position themselves for the future.
To get started, the rule is: Just start!
“Many companies are still undecided,” says MES expert Harald Kimmerle. “People are aware that the future will be digital, they research and evaluate, they plan for the long term, but often nothing much happens.” The risk of being left behind in the competition as a result is great.
In the digital factory, information is exchanged digitally
At the office and management level, digitization has long since made its way through ERP. And in production? Here, everyday life is still dominated by Excel spreadsheets, aisles on the shop floor or the transport of paperwork. The following case study shows how things can be different:
Ms. Maier from production planning receives the order backlog to be scheduled from the ERP. With the support of the MES, she creates the machine assignment for the next two weeks in detailed planning. The terminals of the machines networked with the MES now display the operations she has planned with all the relevant information.
Mobile production data digitally available everywhere
Shift start for the production worker Mr. Schmidt. After he has logged on to the machine terminal, he is directly shown which planned operations are pending. In addition, he can display further linked information such as goods slips or order papers.
During production, the MES continues to collect and store all data such as machine cycles or statuses. These are not only displayed for Mr. Schmidt on the terminal, but also shown via large dashboards for all production employees. This gives everyone a realistic overview of the entire shopfloor. Ms. Maier also automatically receives all information from production. In her planning, the target progress is compared with the actual progress in real time and delays are visualized immediately.
Making quick decisions directly at the terminal
In the event of a malfunction, Schmidt the production worker has to act quickly. Instead of making phone calls or looking for a maintenance employee somewhere, smart networked production offers him much more effective options. For Harald Kimmerle, this also includes optimized information exchange. “With the chat function, we can speed up communication and coordination among those involved in the process.” Decisions made, important information or changes at short notice are quickly transmitted to the production management. “When using the maintenance module, the repair order can be generated directly. This provides an enormous time advantage.”
MES brings the added value
The case study shows that added value can be gained with just a few digitized production areas. However, MES Software not only covers basic requirements, but also offers additional modules for machine maintenance, traceability of products, materials and containers, reporting for production controlling or process data acquisition for the traceability of tempering processes, for example.
Harald Kimmerle, Managing Director of iT Engineering Manufacturing Solutions GmbH confirms, “All factors such as machine inventory, container management or production progress must be connected and a continuous flow of data and information across all resources and processes must be guaranteed in real time.”
With the MES Software EMC, all production processes from order to delivery are described, analyzed and archived with the aim of creating transparency across the entire manufacturing process.
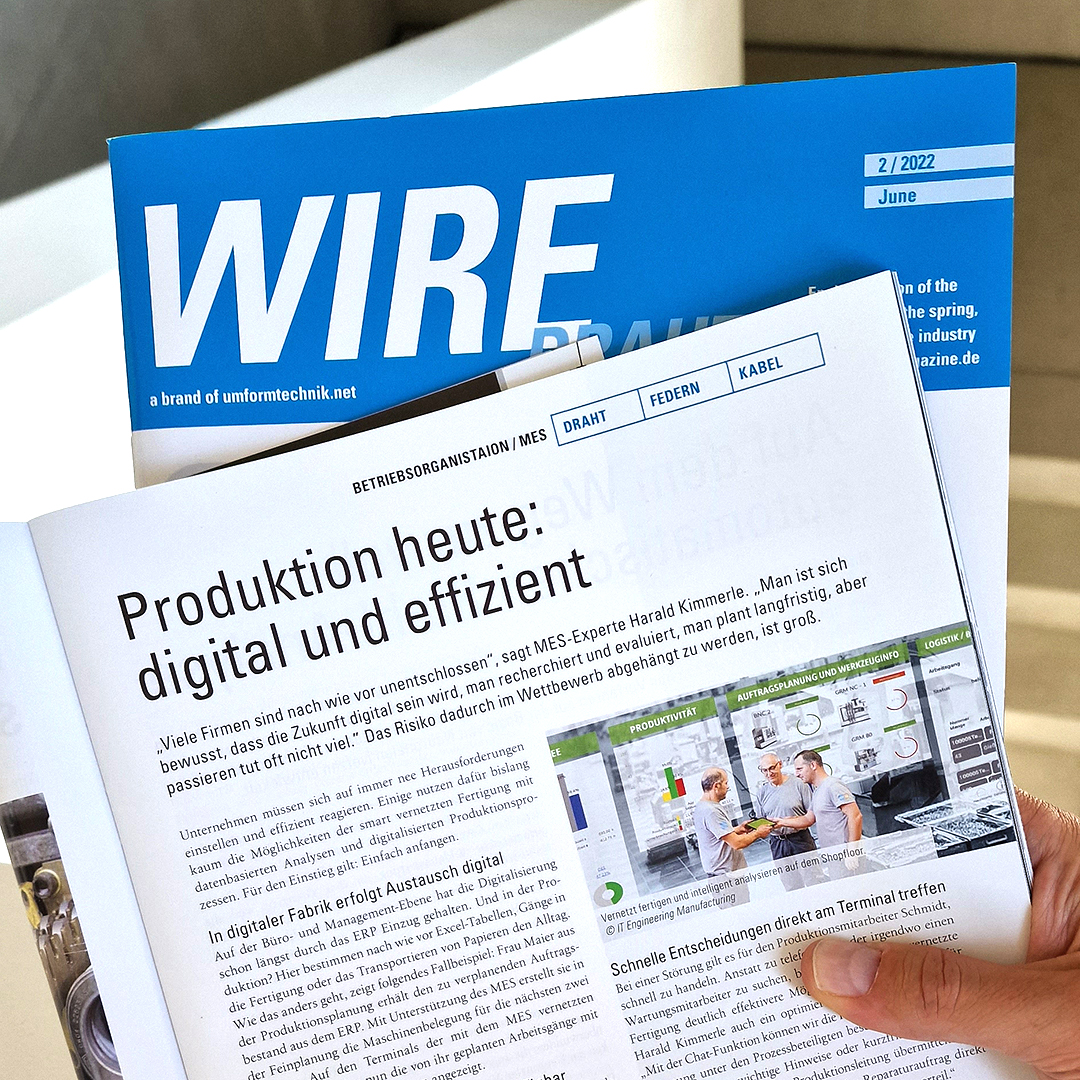