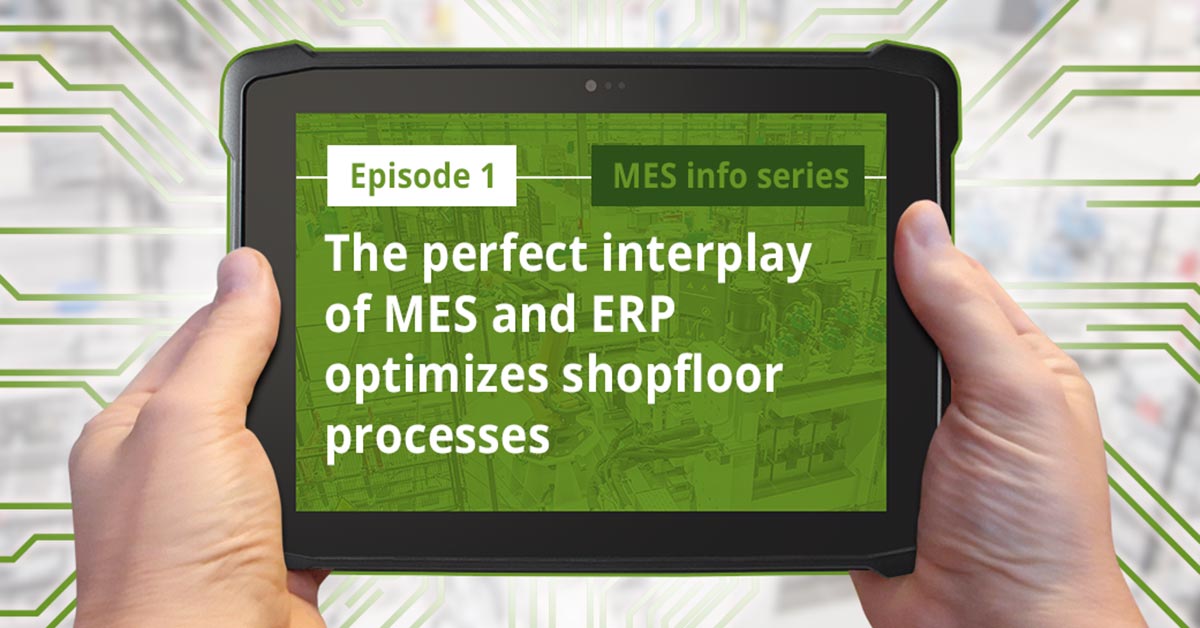
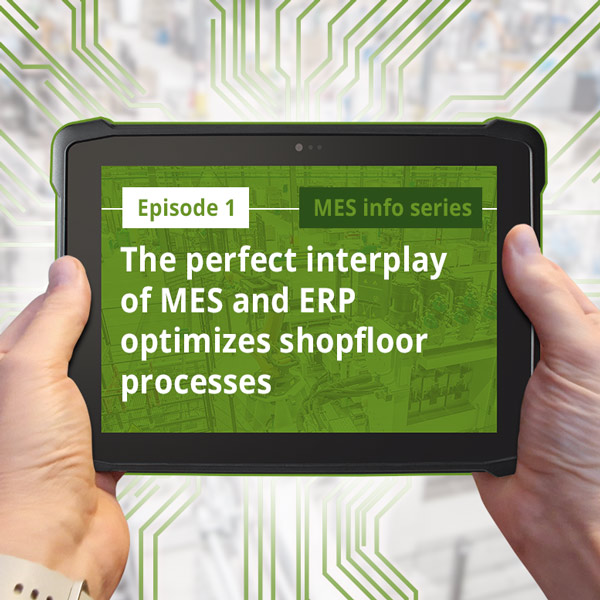
Episode 1 of the MES info series
Every system, whether ERP or MES (Manufacturing Execution System), has its own unique selling points. But while ERP systems are now standard in practice for everything to do with order management or work planning, many companies do not realize the potential offered by the interplay of ERP in combination with a smart MES solution.
The digital, smart networked factory supplements the functions of the ERP solution with real-time data from production and combines them profitably. In addition, the MES enables access to a lot of production-relevant information and important data from the ERP directly in production and back. This interaction across many areas of a company can significantly increase productivity in production and sustainably optimize processes.
In episode 1 of our MES info series about digitalization, we will show you how MES and ERP are connected and how many processes and procedures can be quickly and easily optimized through their connection and data exchange.
The perfect interplay of MES and ERP
optimizes shopfloor processes
The perfect interplay of MES and ERP optimizes shopfloor processes
MES and ERP in dialog
The bidirectional exchange between ERP and the MES system ensures that all data can be used anywhere without loss and reliably. The MES Software EMC is compatible with all common ERP solutions and thus guarantees perfect interaction. The data flows in both directions. In other words, from the ERP to the machine control system and back again.
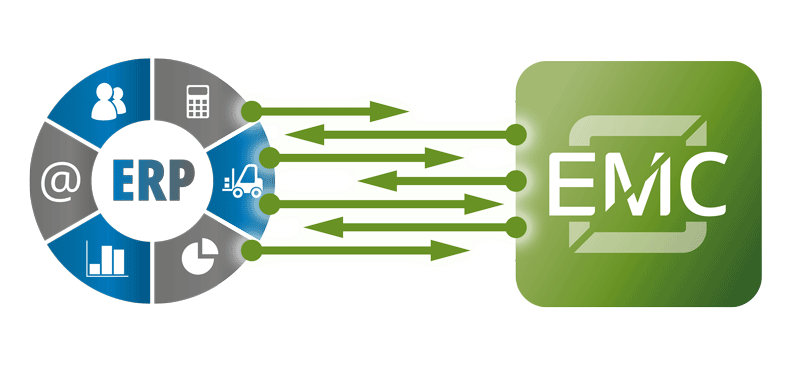
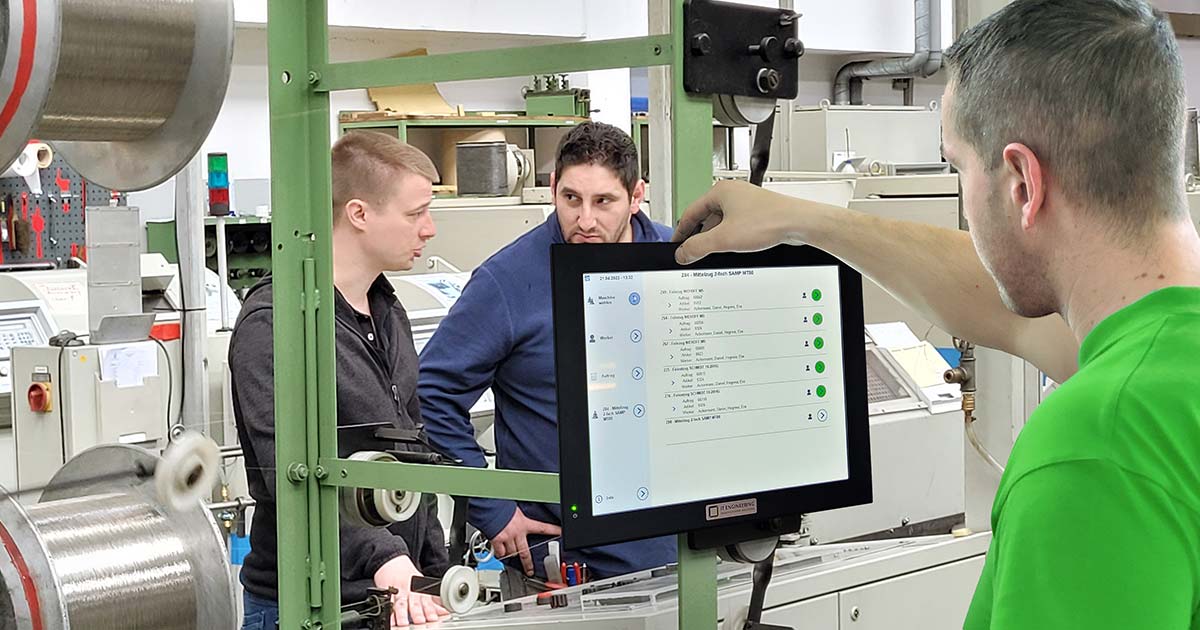
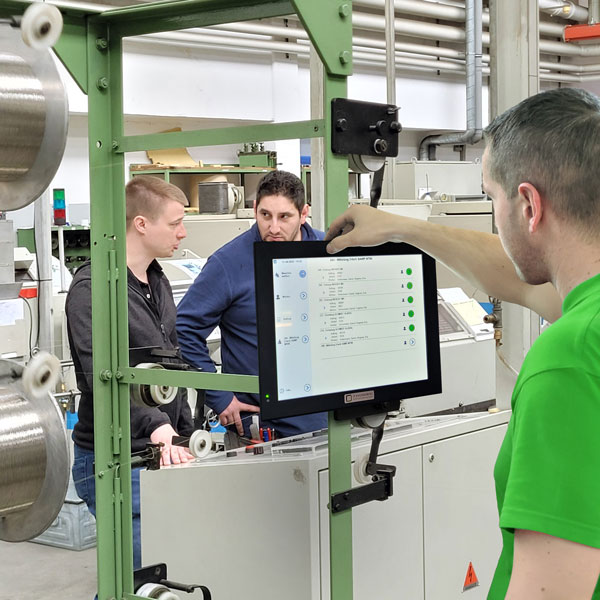
Send order data from the ERP down to the machine control
With the connectivity of MES and ERP, it takes just one click to send the necessary data for the planned orders digitally to the machine control system. The employee at the machine can see all important order-related information in detail on the MES terminal, such as the current status of orders and work processes, interruptions and order progress, comparison of target and actual values or even the order backlog and order sequence. Like that, overproduction is immediately recognizable.
An example: The MES continuously compares the ERP specifications with the current progress. If the digital machine data acquisition (MDA) by the MES Software EMC registers overproduction because the machine simply continues to run, this information is reported directly back to the ERP. This significantly increases responsiveness and reduces unnecessary overproduction.
Direct connection of machines and workstations
Using OPC-UA or smart IoT modules, all machines, whether new or old, can be easily connected directly. Operational data is recorded digitally during operation directly at the MES terminal. This means that manual or semi-automated workstations are also connected to the ERP.
Automated feedback to the ERP
All data recorded, manually at the terminal or automatically from the machine, is reported directly back to the ERP system. On the one hand, this includes classic production data such as the good quantity, rejects or, in the case of rework, the reason or the time required. On the other hand, the MES Software EMC also reports machine and order times back to the ERP. This includes, among other things:
- Reasons for downtime
- Set-up, idle and production times
- Occupancy rate taking into account the working time model
- Automated time off booking
This guarantees that the same “knowledge” and all information is available at all levels.
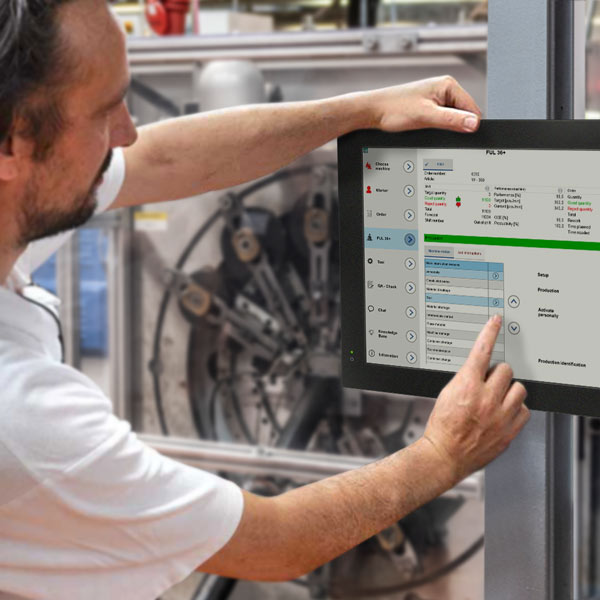
Rapid effects of digitalization
The positive effects of the integration between the two systems quickly become apparent. The processes on the shopfloor are shortened and optimized. The connection supplements the ERP system with valid, automatically recorded data. This provides transparency for the entire company and increases responsiveness, for example in the event of production delays.
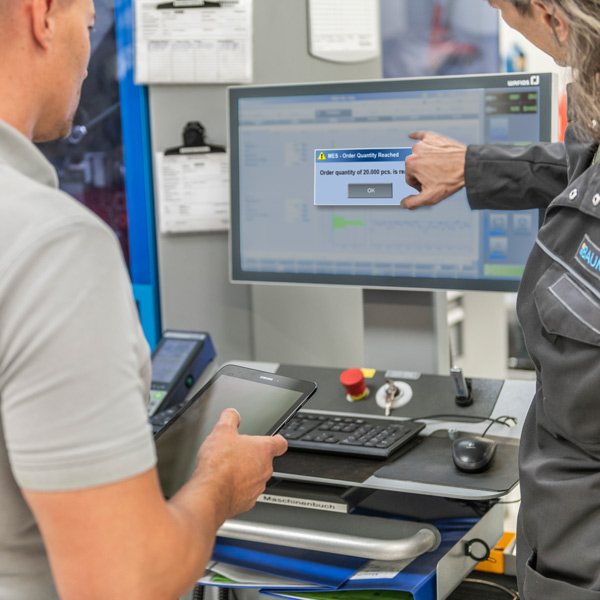
Smart monitoring of production
Depending on the OPC-UA interface and its capabilities, the automated production monitoring system can display information or notifications immediately.
For example, when the order quantity is reached, this is shown directly on the machine display via a window. This enables rapid intervention and prevents unnecessary overproduction.
Complete documentation
The interconnection of MES and ERP enables complete and seamless documentation of process data of varying quality. Values such as energy, air, temperature or rotation speeds are important indicators for evaluating your own production and form the basis of a continuous improvement process. Valuable conclusions can be drawn from them, processes can be analyzed and potential for improvement can be easily identified and documented.
Conclusion Episode 1
MES and ERP: one does not exclude the other. However, the combination of both systems offers great potential for manufacturing and production efficiency.
As the same data forms the basis of the interconnection, synergies are created that sustainably facilitate working methods and processes both on the shopfloor and in control or management. The automated exchange makes many manual entries and processes superfluous. In addition, required data can be transferred from A to B and back again in real time – paperless and complete. All data is anchored in the system, guaranteeing that it can be found and retrieved quickly for future orders.