Implement digitalization in manufacturing successfully
It is fundamentally clear that it is difficult to operate entirely without digitalization in today’s industry. Standard processes such as classic Machine Data Acquisition (MDA) or the use of an ERP system are widespread and do their job. People often don’t even know how to tackle all the issues surrounding digitalization in manufacturing and modern production. However, digitalization in the sense of Industry 4.0 production offers so many more possibilities and enables great potential in terms of efficiency and productivity across all areas.
Digitalization can be so easy
Unlike an ERP, which can often be lengthy and difficult to implement, our MES Software EMC and its standardized module EMC.Converter make it easy to digitalize your production with very little effort and in just a few weeks.
Acquiring the data is just the beginning. EMC enables the basis for the Smart Factory, in which all players involved in production are connected. It offers the perfect digitalization concept and is the basic prerequisite for ensuring that all relevant data is consistently recorded and processed in a user-oriented manner. Of course, this not only applies to the data collected directly from the machines. The automated, bidirectional exchange of ERP and machine control reliably generates information flows for all processes involved in production. All with the goal of enabling efficient production and manufacturing.
This includes, for example
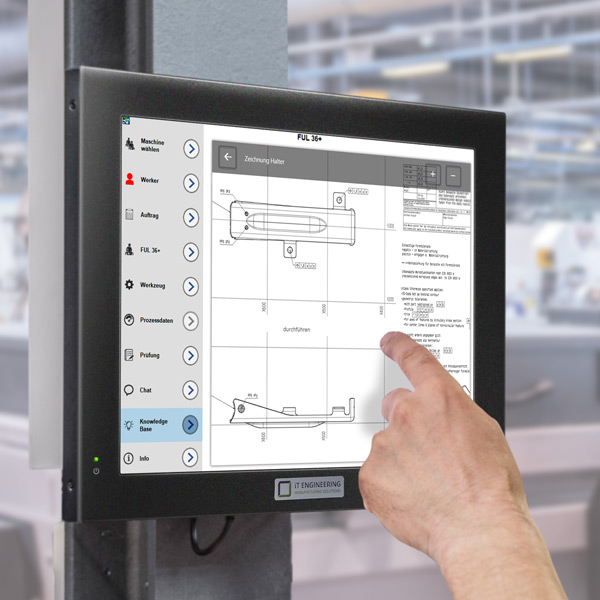
Paperless manufacturing: Provide order-relevant information such as drawings digitally everywhere
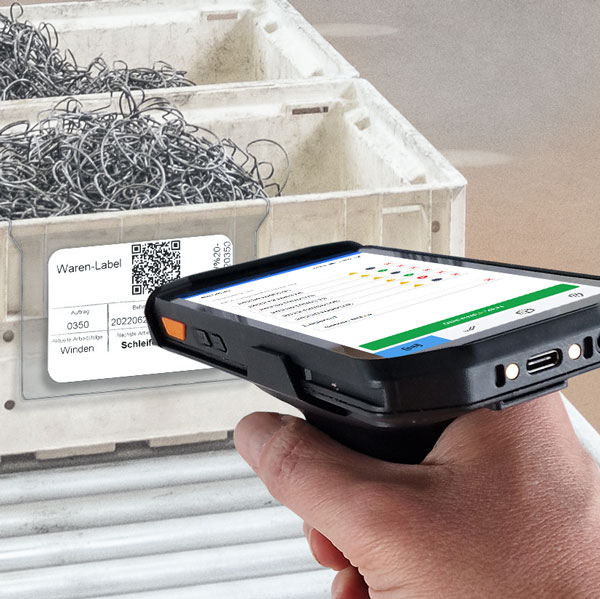
Seamless traceability: Easily retrieve information via QR code and track containers, batches and products
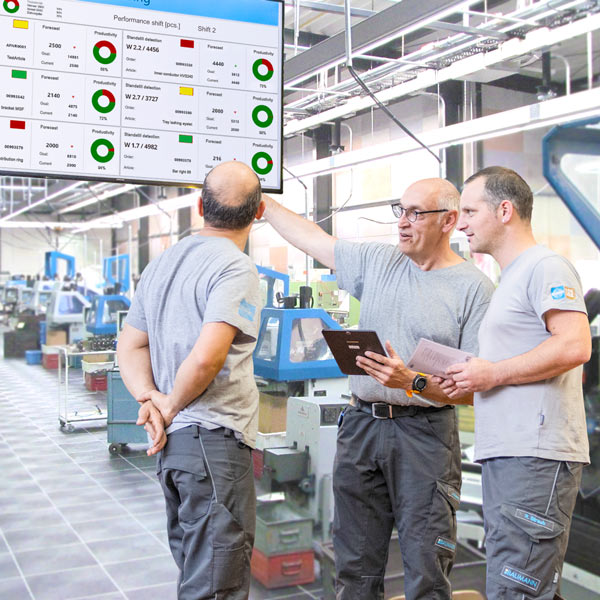
Digital shopfloor management and dashboards: everyone knows the current status of production in real time
Four chances of digitalization for a smart networked production
Many processes and functionalities are directly interrelated or complement each other. It is therefore worth taking a closer look at how the smart factory for discrete manufacturing works in detail, how data gets to exactly where it is useful and how this results in synergies for many areas of production.
In a multi-part series, we will show you how smart networking in the digital factory simply works and how you can take advantage of the chances offered by digitalization. What opportunities does the digitalization of production processes offer? How can this sustainably increase productivity and efficiency in your production?
The individual episodes of this series will be released gradually. We will be happy to inform you of each new episode by email. Simply subscribe to our newsletter.
Overview of the individual episodes
Overview of the individual episodes
Digitalization implemented step by step
Simply achieve more digitally
The modular architecture of the innovative MES Software EMC from iT Engineering Manufacturing Solutions GmbH enables reliable digitalization of production processes and their optimization. The freely combinable modules and functionalities are seamlessly compatible with each other and thus enable a holistic digitalization concept.
Digitalization Episode 1
The perfect interplay of MES and ERP
optimizes shopfloor processes
The perfect interplay of MES and ERP optimizes shopfloor processes
Every system, whether ERP or MES (Manufacturing Execution System), has its own unique selling points. But while ERP systems are now standard in practice for everything to do with order management or work planning, many companies do not realize the potential offered by the interplay of ERP in combination with a smart MES solution.
The digital, smart networked factory supplements the functions of the ERP solution with real-time data from production and combines them profitably. In addition, the MES enables access to a lot of production-relevant information and important data from the ERP directly in production and back. This interaction across many areas of a company can significantly increase productivity in production and sustainably optimize processes.
In this first episode about digitalization, we will show you how MES and ERP are connected and how many processes and procedures can be quickly and easily optimized through their connection and data exchange.
MES and ERP in dialog
The bidirectional exchange between ERP and the MES system ensures that all data can be used anywhere without loss and reliably. The MES Software EMC is compatible with all common ERP solutions and thus guarantees perfect interaction. The data flows in both directions. In other words, from the ERP to the machine control system and back again.
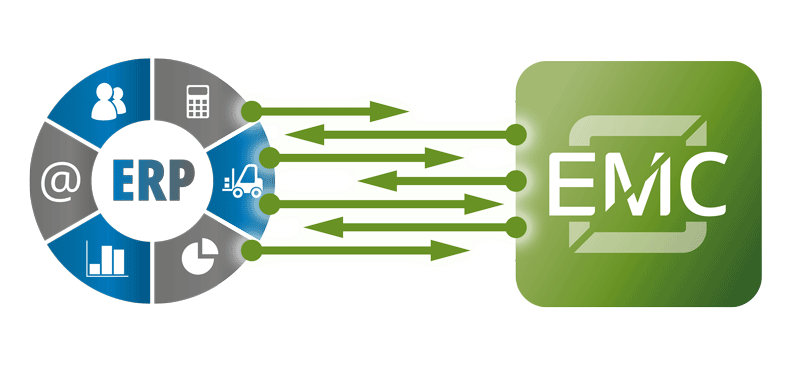
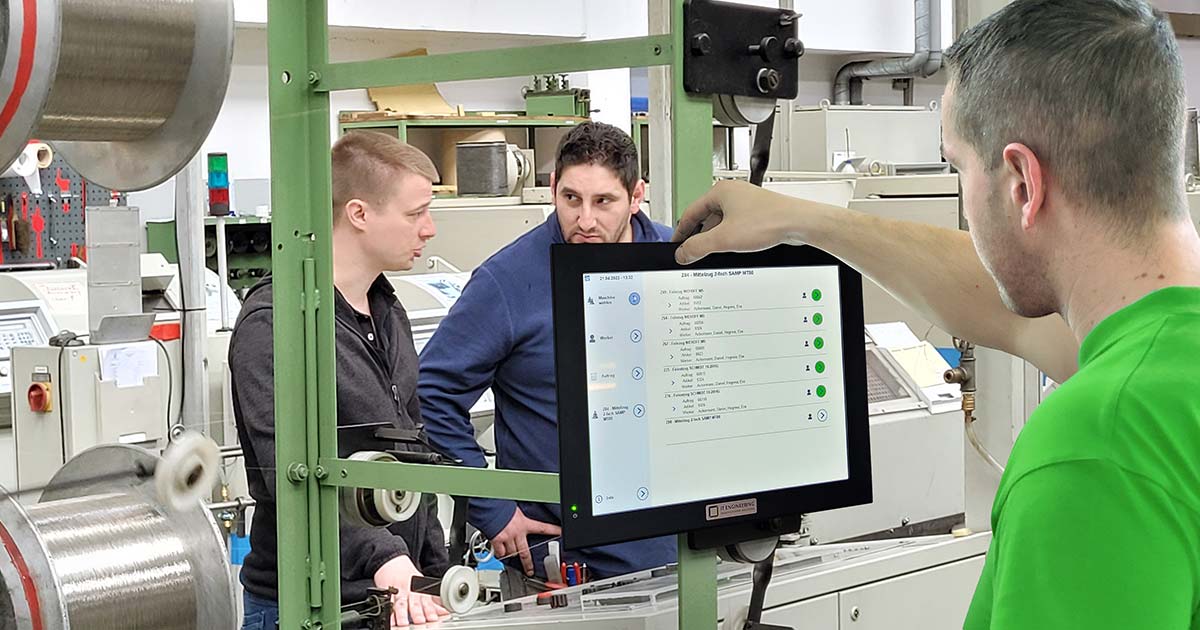
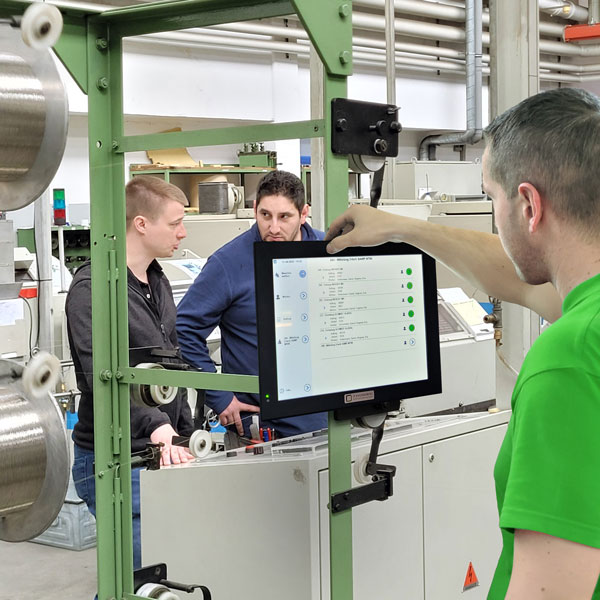
Send order data from the ERP down to the machine control
With the connectivity of MES and ERP, it takes just one click to send the necessary data for the planned orders digitally to the machine control system. The employee at the machine can see all important order-related information in detail on the MES terminal, such as the current status of orders and work processes, interruptions and order progress, comparison of target and actual values or even the order backlog and order sequence. Like that, overproduction is immediately recognizable.
An example: The MES continuously compares the ERP specifications with the current progress. If the digital machine data acquisition (MDA) by the MES Software EMC registers overproduction because the machine simply continues to run, this information is reported directly back to the ERP. This significantly increases responsiveness and reduces unnecessary overproduction.
Direct connection of machines and workstations
Using OPC-UA or smart IoT modules, all machines, whether new or old, can be easily connected directly. Operational data is recorded digitally during operation directly at the MES terminal. This means that manual or semi-automated workstations are also connected to the ERP.
Automated feedback to the ERP
All data recorded, manually at the terminal or automatically from the machine, is reported directly back to the ERP system. On the one hand, this includes classic production data such as the good quantity, rejects or, in the case of rework, the reason or the time required. On the other hand, the MES Software EMC also reports machine and order times back to the ERP. This includes, among other things:
- Reasons for downtime
- Set-up, idle and production times
- Occupancy rate taking into account the working time model
- Automated time off booking
This guarantees that the same “knowledge” and all information is available at all levels.
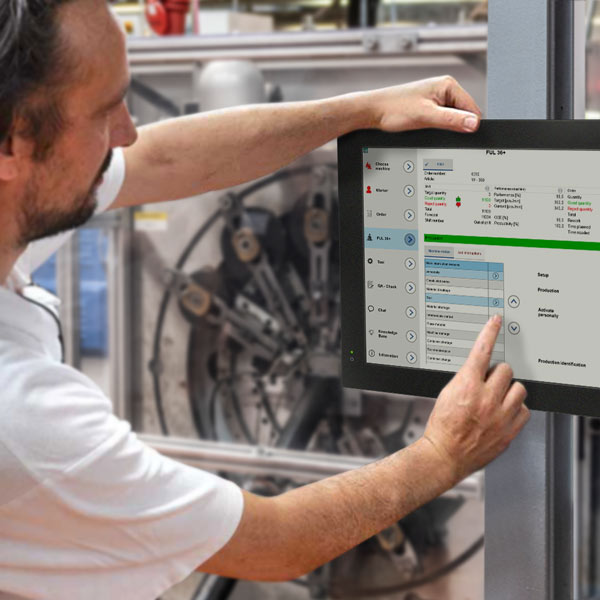
Rapid effects of digitization
The positive effects of the integration between the two systems quickly become apparent. The processes on the shopfloor are shortened and optimized. The connection supplements the ERP system with valid, automatically recorded data. This provides transparency for the entire company and increases responsiveness, for example in the event of production delays.
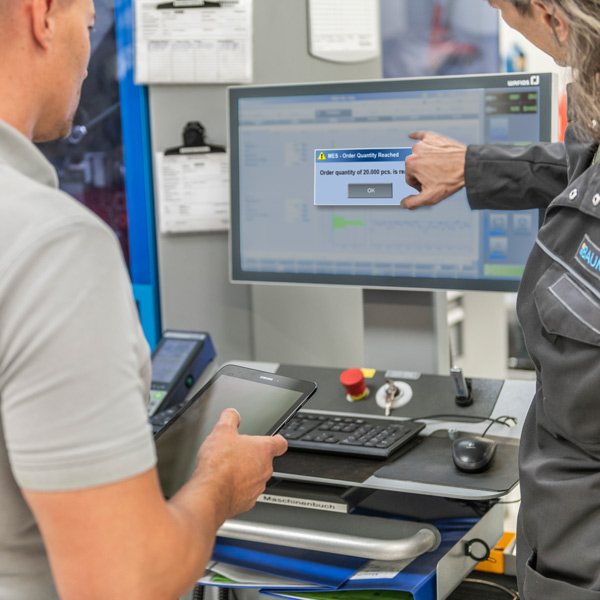
Smart monitoring of production
Depending on the OPC-UA interface and its capabilities, the automated production monitoring system can display information or notifications immediately.
For example, when the order quantity is reached, this is shown directly on the machine display via a window. This enables rapid intervention and prevents unnecessary overproduction.
Complete documentation
The interconnection of MES and ERP enables complete and seamless documentation of process data of varying quality. Values such as energy, air, temperature or rotation speeds are important indicators for evaluating your own production and form the basis of a continuous improvement process. Valuable conclusions can be drawn from them, processes can be analyzed and potential for improvement can be easily identified and documented.
Conclusion
MES and ERP: one does not exclude the other. However, the combination of both systems offers great potential for manufacturing and production efficiency.
As the same data forms the basis of the interconnection, synergies are created that sustainably facilitate working methods and processes both on the shopfloor and in control or management. The automated exchange makes many manual entries and processes superfluous. In addition, required data can be transferred from A to B and back again in real time – paperless and complete. All data is anchored in the system, guaranteeing that it can be found and retrieved quickly for future orders.
Digitalization Episode 2
Digital shopfloor management for more transparency,
better collaboration and more efficient processes
Digital shopfloor management for more transparency, better collaboration and more efficient processes
Every production process is dynamic. And there are countless variables that determine how productive or effective production is. In the digital factory, these variables in the form of real-time information or real-time data are the constant basis for the ongoing progress of production. Data such as utilization rates, OEE, the most common reasons for errors, employee productivity or energy figures are essential for assessing the efficiency of your own production.
Access to and availability of real-time information brings many advantages. On the one hand, the status of current production can be compared with the specifications from order planning and the ERP at any time. Secondly, it actively helps to identify disruptions and deviations in the processes and to take action at an early stage. To make this possible, our MES Software EMC reliably records and bundles all real-time data on the shopfloor and uses it as required – for example as real-time dashboards of ongoing production, in the planning of machine utilization, in analysis or in the creation and distribution of reports.
In this second episode of our MES info series, we will show you how digital shopfloor management can make your production more effective and transparent and thus also ensure better collaboration.
Know, what’s going on
Both the actual value of the current production and the target value of the order are displayed directly on the MES terminal at the machines at all times. The worker can see the current order progress at a glance and can intervene if necessary. Thanks to the rapid intervention, regular operation is restored promptly, resource utilization is increased and deadlines are met.
You can find out how the data from the machines and workstations is recorded in episode 1 of our MES info series.
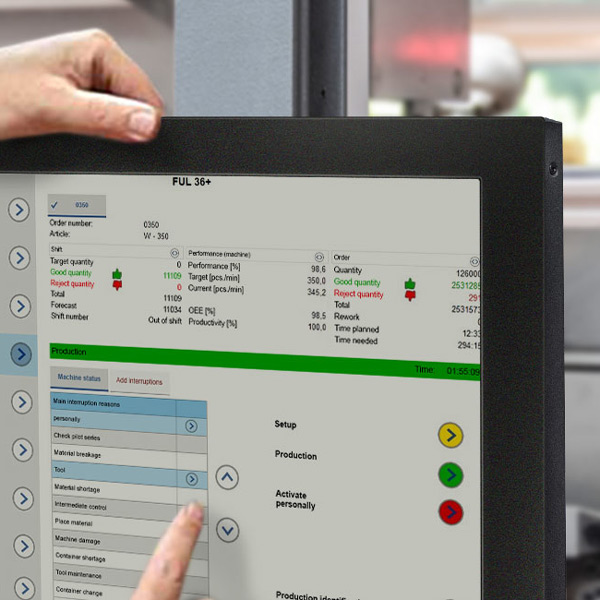
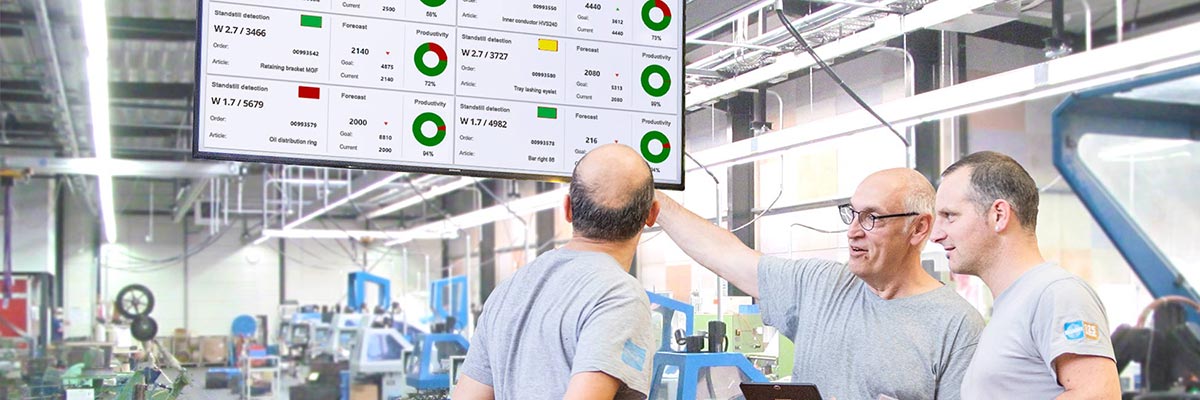
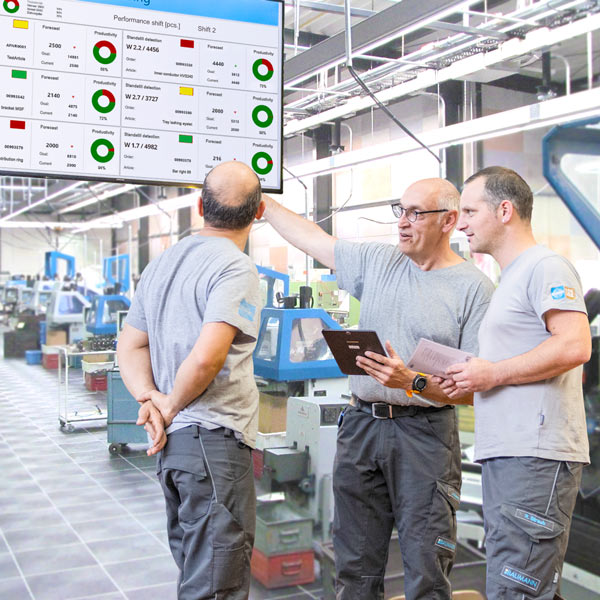
Increasing efficiency begins with recognizing the need for action
Always have a simple and intuitive overview of ongoing production. Meaningful key figures are visualized with the help of individual dashboards both on the desktop and on large screens directly on the shopfloor. This means you always have an overview of the current order progress, key production figures such as OEE or productivity. Directly in your dashboards and in real time.
This allows you to immediately identify machine downtimes, reduced speed, quality losses and system malfunctions. Potential sources of error are visible at an early stage and countermeasures can be initiated promptly.
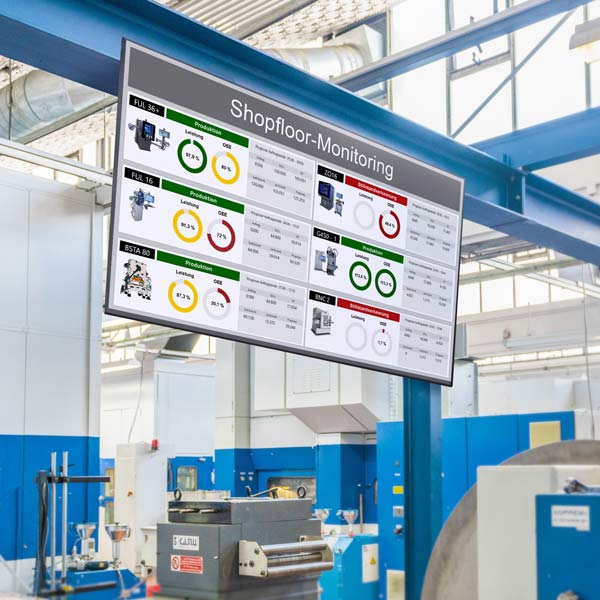
Productivity is driven by structured and systematic action
The visualization of real-time information directly on the shopfloor supports your employees in the structured and targeted implementation of measures. They have an overview of the progress of production at all times.
They can also easily check whether decisions made or measures taken are effective.
This transparent presentation of ongoing production via dashboards sustainably improves collaboration and communication between employees. All with the aim of achieving more more quickly together.
Sustainable optimization of processes through continuous improvement
The real-time information directly from production enables realistic analyses and reports. This not only allows you to compare orders or machines, but also to quickly identify risks and potential through important analyses such as OEE of systems, setup levels, system downtimes, planned/actual time analyses of articles or productivity indicators.
EMC.Reporting enables you to carry out an honest performance analysis and process optimization of production based on sound machine and production data. This enables systematic root cause analyses to be carried out.
With the help of well-founded corrective measures and effectiveness checks, improvements are integrated into your company processes on a sustainable and continuous basis.
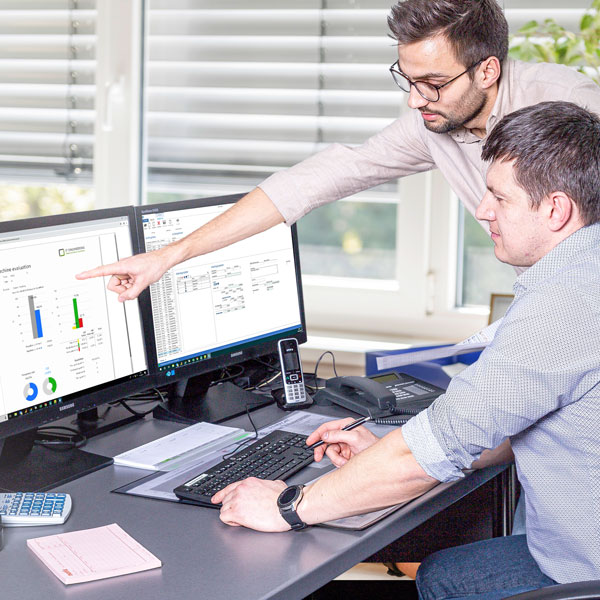
Automated report distribution
A large number of reports can be generated from the real-time data and automatically distributed to the relevant employees or departments.
The systematic execution of analyses and evaluations with the system reports shows cause and effect in process management and controlling. Give your employees the opportunity to analyze their data, gain important insights and make better decisions. This means that success can be measured at any time and in real time.
Conclusion
Real-time information is the gold of any production. It enables efficiency and productivity to be actively displayed and evaluated at any time. The real-time production data collected is used precisely where it is useful. This makes working methods easier in the long term.
Thanks to the significantly increased level of transparency regarding ongoing production, you always know where which order is running with which item and with what progress. Delays are immediately visible, problems with material, articles or tools are quickly detected and enable a prompt response.
The knowledge gained from the recorded real-time data is permanently anchored in the system and thus offers the opportunity to gain in-depth analyses of your own production. Important adjustments can thus be found and optimized quickly. With digital shopfloor management, nothing stands in the way of a continuous and sustainable improvement process.
Digitalization Episode 3
Optimize workflows quickly
and simplify your container logistics
Optimize workflows quickly and simplify your container logistics
“We’ve always done it this way.” Everyone knows this statement when it comes to why certain workflows and processes work or don’t work the way they do. And many “old familiar” processes that have been in place for years are anything but effective, productive or sustainable. In reality, many resources (time, money, materials, etc.) are wasted as a result. This is precisely where the digital factory comes in and is the perfect tool for quickly simplifying and optimizing processes and workflows in production.
And this happens across many areas of production. With the EMC Knowledgebase module, for example, the physically printed work folder is simply replaced digitally. The worker receives all the information they need, such as drawings or work instructions, conveniently at the machine terminal – complete and paperless. And they can add their own information directly.
This digital bundling of information also makes it possible, for example, to replace the typical goods or container label, which always had to be printed out blank and laboriously filled in by hand. All information is available in the system. The label can be printed out directly at the workstation using mobile printer hardware, allowing the container to be perfectly labeled.
This pays off when it comes to complete traceability in production. Clean processes are immensely important here. In the digital factory, containers are labeled automatically using the recorded and stored data or according to specifications from the ERP. By scanning QR codes on the goods label, products, batches and containers can be reliably localized.
In the third episode of our MES info series on the topic of digitalization, we show you how you can quickly optimize many workflows in your factory with simple means and thus simplify container logistics in the long term, for example.
Simplify and optimize workflows
By simply and digitally providing relevant information and documents for each order, production processes can be sustainably optimized and simplified. With EMC KnowledgeBase, for example, article drawings or plans can be displayed directly at the machine. Digitally and at the touch of a button, directly at the MES terminal in production or on a mobile tablet.
The employee at the machine no longer has to rummage through documents, but has quick and efficient access to the information required for his work. All important documents relating to both the order and the machine are stored digitally. Separate order or article folders with printouts of this information are therefore no longer necessary.
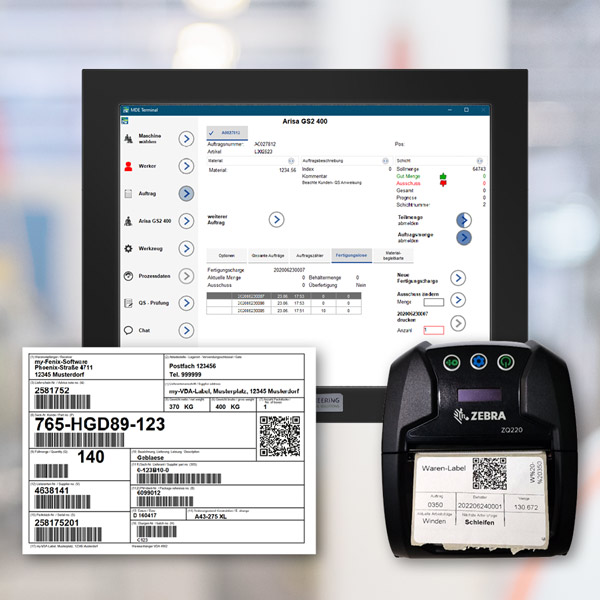
Print out the goods label directly on site
The digital factory offers the option of printing out the goods label directly at the machine when the container is full. This is done manually or automatically by the machine or a container changer. The quantities are taken from the Machine Data Acquisition and simply move along as information.
The stored and recorded information is anchored in the MES Software EMC system and assigned to each order. This means that this information travels with each container and can be called up at any time using a QR code. In addition to the order and container number, it can also contain the quantity, the current and next work sequence and other information relevant to your production, such as the location.
This enables clear, digital identification of the parts and containers and thus seamless traceability.
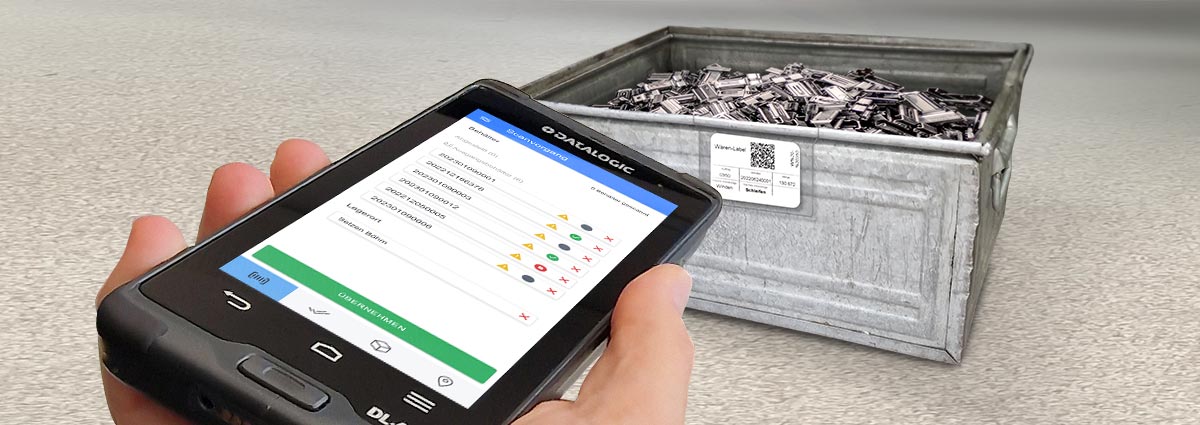
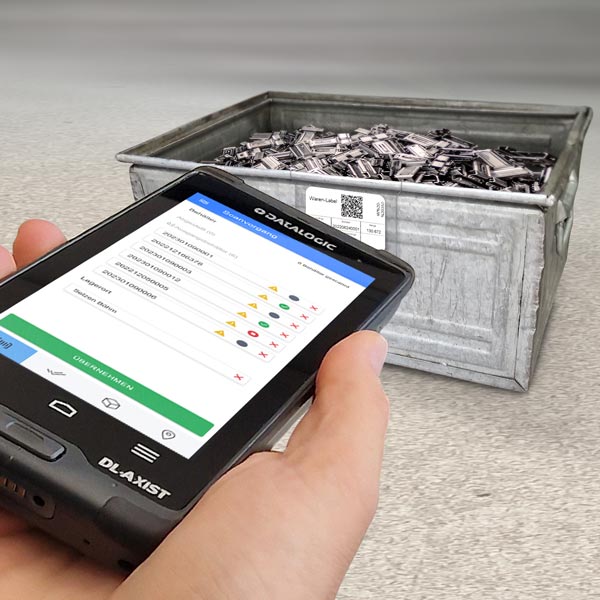
Simplify container logistics in production
Each container is given a unique container number in EMC FactoryLogistics, either specified by the ERP or generated directly at the MES terminal for each order. Once the order has been completed, the container is emptied and assigned a different label for the next order. This makes it easy to localize each container (at the machine, in the interim storage area, etc.). Typically, containers are identified using barcodes, QR codes or RFID.
Intralogistik 4.0
This is how container and transport organization works in the digital factory: For each work step, the containers are clearly identified and registered as incoming or outgoing containers – including the individual work steps and intermediate storage locations. The incoming and outgoing containers are stored and managed for each work step of a production order.
This makes the location of the semi-finished parts transparent for everyone. No more searching for containers.
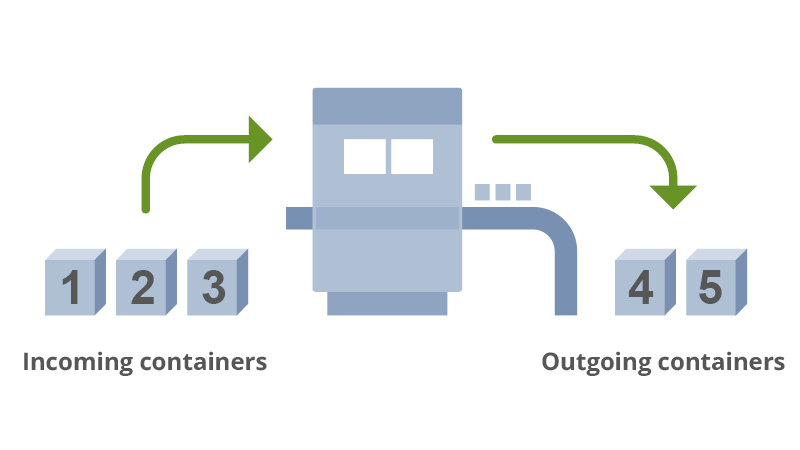

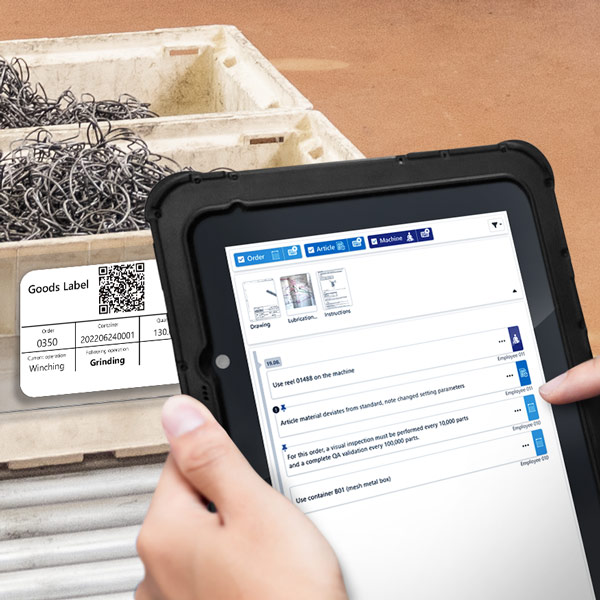
Paperless and digitally identifiable
In the digital factory, the combination of the EMC FactoryLogistics and EMC KnowledgeBase modules enables additional stored information to travel with each container in addition to the unique identification. Scanning the QR code provides the same drawings, information and documents at any time. This means that everyone has the same data and information as a basis. This guarantees maximum transparency, efficiency and traceability and makes a lasting contribution to quality assurance in production.
Conclusion
The digitalization of processes can quickly simplify and optimise some workflows in production. Relevant information and knowledge from production can be used in a variety of ways. This simplifies working methods and enables errors and weak points to be eliminated. As all important information is bundled and available, printouts, order folders or forms that have to be filled out by hand are no longer necessary and an important step towards sustainable and almost paperless production and manufacturing.
Container logistics in particular benefit significantly from this. Information travels automatically and sensibly and ultimately ensures that products, containers and batches can be reliably traced at all times. It takes the complexity and error-proneness out of container management. And it guarantees that all relevant information is always available – at the machine, for the individual employee and when locating the containers.
Digitalization Episode 4
Realistic planning of machine occupancy
with real-time data and maintenance
Realistic planning of machine occupancy with real-time data and maintenance
Proper planning of machine occupancy is immensely important for efficiency and productivity. And one of the biggest challenges in production is keeping the machines running and thus avoiding production delays.
Rough planning with orders from the ERP assumes infinite production capacity. However, what happens live in production, e.g. during a repair or maintenance, does not initially influence this rough planning. In many places, this is done using Excel lists that are laborious to maintain, which have to be corrected daily and constantly reconciled. The effort involved is enormous and the sources of error are high.
This is not the case in the digital factory. Thanks to the direct connection to the machines, the detailed planning of machine allocation always takes into account real-time data directly from production. This means that if the machine stops, for example if a tool breaks, the planning automatically adapts and reliably reschedules follow-up orders. Predefined maintenance and repairs are also taken into account and scheduled correctly.
In the fourth episode on the topic of digitalization, we will show you how you can achieve realistic, resource-optimized planning of machine occupancy using real-time data and the integration of maintenance and repairs.
Machine occupancy planning with direct connection to the machine
Realistic production planning for machine utilization is the be-all and end-all. This is made possible by the direct connection to the machines. The roughly planned orders are received by the ERP and supplemented and adjusted in short-term planning with the data collected in real time on the shopfloor (machine occupancy, tool allocation, employees or downtime reasons). The work processes for the orders are then planned for the individual resources (machines, workstations).
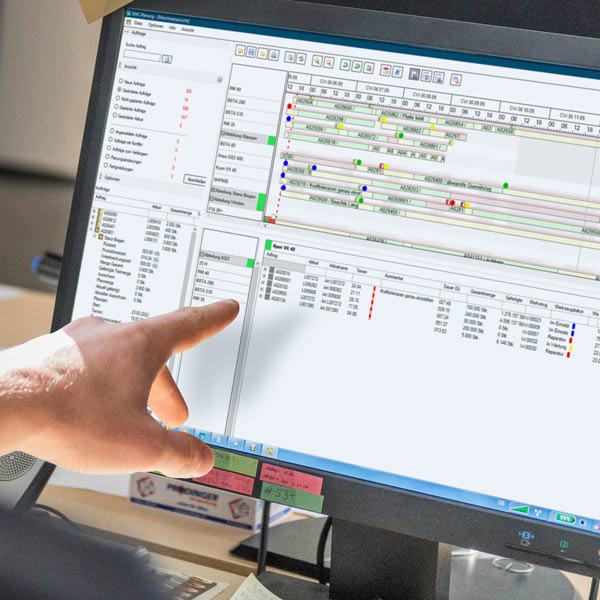
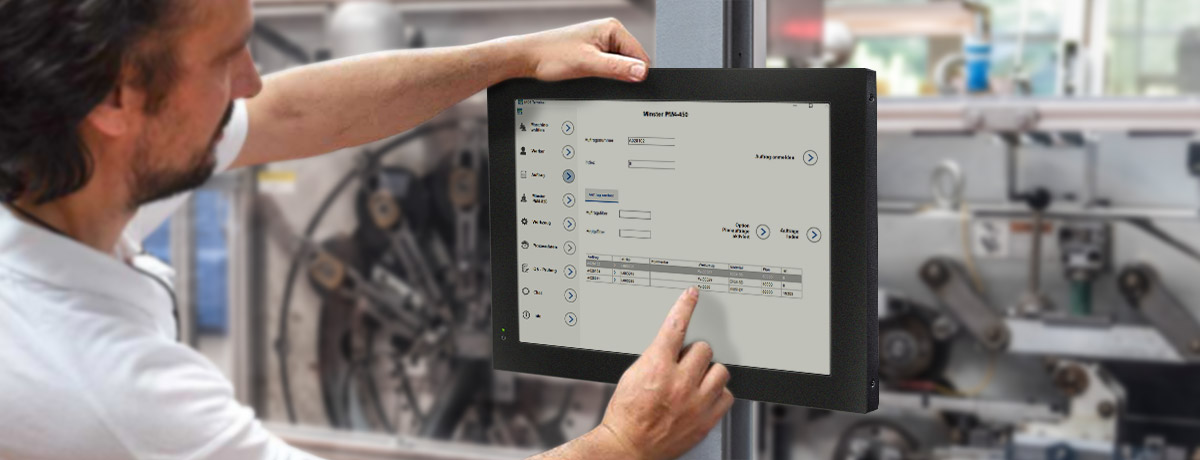
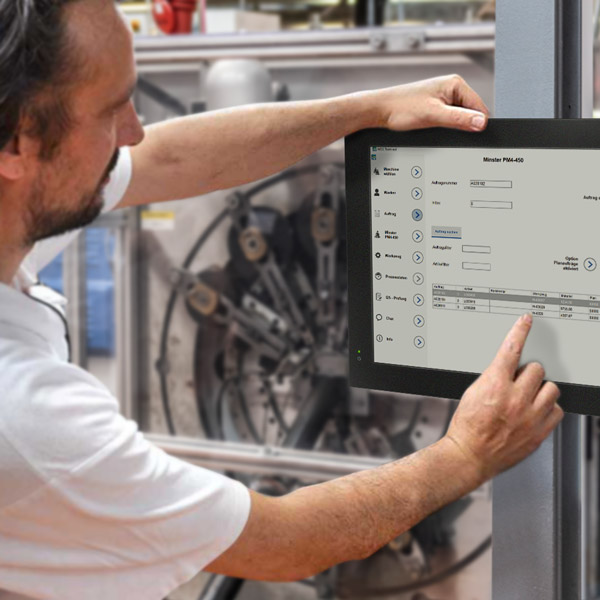
Bye-bye printed planning lists
Planning in digital production makes printed production lists and their distribution in production superfluous. This means that the current plan sequence is displayed directly on the MES terminal and in the shopfloor dashboard. In addition, the order is registered directly via the displayed planning list.
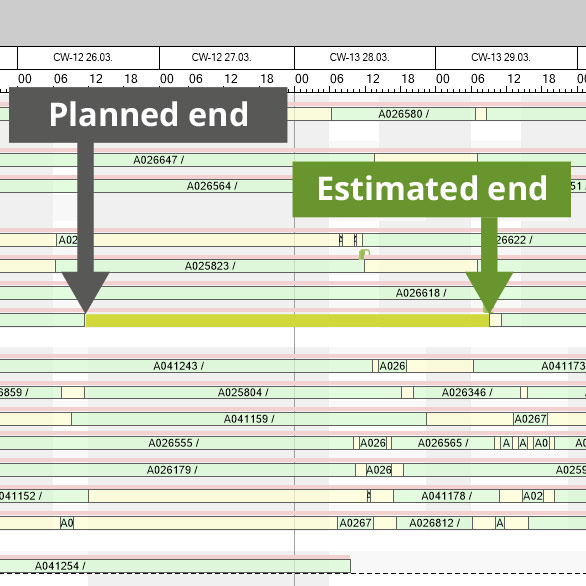
Get to your goal smarter with the navigation function
The navigation function automatically adapts your planning to the current order progress of the machine and visualizes the planned order sequence digitally on the machines.
The actual progress is continuously reported back to the planning after the start of the order on the machine – in real time. The planning is then updated automatically, carries out a forecast calculation for the end of the order and updates the start date of the following orders.
In addition, predefined machine or tool maintenance is automatically taken into account in the machine document planning and the planning is adjusted accordingly.
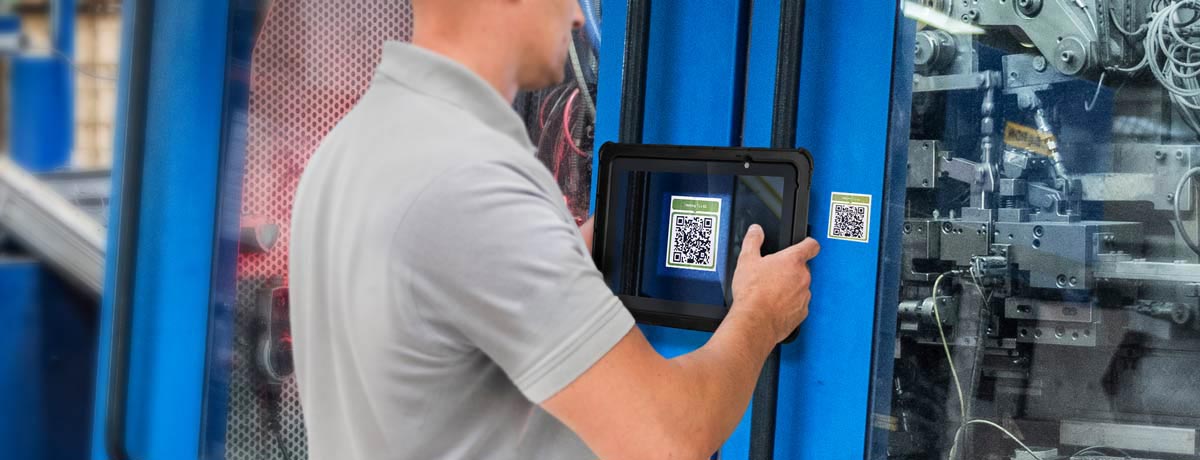
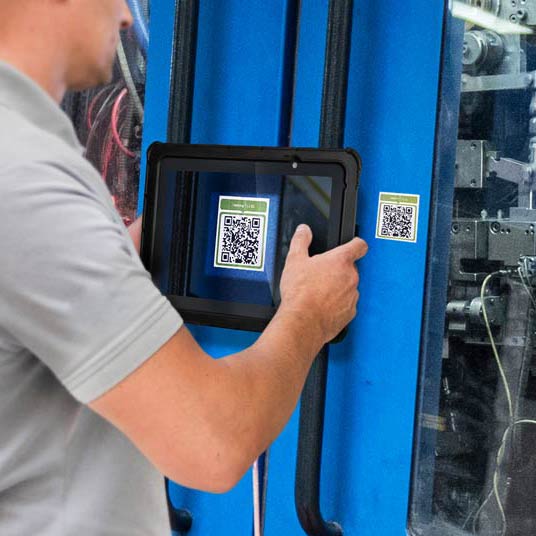
Keeping the machines in optimum condition
It goes without saying that machines need to be regularly serviced, checked and maintained. This has a lasting effect on the quality of your own production and ensures that the machines run smoothly. The EMC.maintenance module makes it easy to neatly file and document important machine maintenance.
Instructions, maintenance steps or special maintenance procedures can be stored for each machine and peripheral equipment – both automatically and manually. In addition to the individual maintenance steps to be carried out, maintenance cycles (daily, weekly, monthly, annually, etc.) can also be defined individually. Typical checks or maintenance tasks, such as a grease change on the gearbox, are also created as maintenance tasks and can therefore be easily carried out and documented as required.
The system continuously checks the status of the machines and reports upcoming maintenance. If maintenance is due, it can be started simply by scanning a QR code attached to the machine, for example.
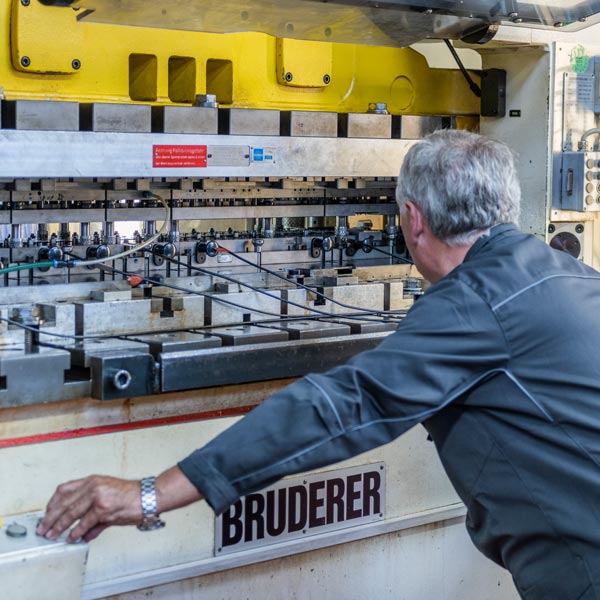
Digitized tool maintenance
With the EMC maintenance module, you can carry out maintenance, repairs and servicing, including all components and spare parts used, both manually and according to individually predefined maintenance cycles. This enables high technical availability and reliable maintenance.
More efficient production and planning with the integration of tool maintenance
The digital information exchange and access provided by the MES Software EMC enables predictive control of individual production processes. For example, in the event of a repair, the toolmaking department is informed directly from the machine terminal. This information is also sent directly to production planning without any detours.
This means that the planner knows the current tool status at all times. Upcoming maintenance and current repairs are automatically integrated into detailed planning. This ensures realistic and smooth production processes. In addition, the tool shop receives information from planning about which tool is needed when and what maintenance is due.
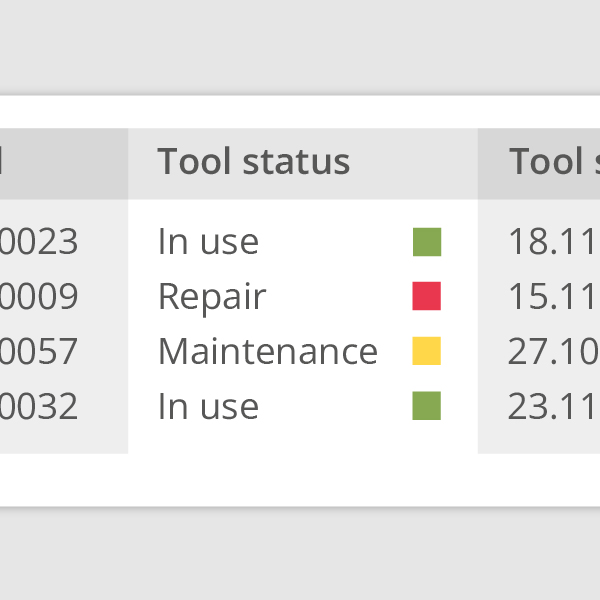
Digital maintenance management
The documentation of maintenance and repairs is complete and comprehensive. All machine maintenance, tool maintenance and repairs are documented in the digital life cycle card of the MES Software EMC. The current status, availability and history of the tools are also stored in the digital tool card.
Further information such as articles and orders are linked. Installed spare parts and their number can be traced exactly.
The complete workflow for digital maintenance management can be called up digitally at any time, directly at the machine terminal or via mobile tablets. Maintenance can be easily started either manually via the portal of the MES Software EMC or by scanning a QR code attached to the machine or tool.
Intelligent analysis
Which tool inserts are responsible for production downtimes? Which spare part is replaced most frequently? How many benders are kept in stock for a production run?
Thanks to the complete, digital recording of inserts or spare parts, for example, the tool design department can access a lot of data to optimize the tool. This makes a significant contribution to increasing productivity and effectively avoiding machine downtime due to unplanned maintenance.
Conclusion
There will always be delays in production and they are difficult to avoid. How these are dealt with and what measures are taken to reduce them makes a decisive difference to how well planning works and therefore how productive and efficient production is.
Resource-optimized planning with the integration of real-time data from production and properly scheduled maintenance ensures that unnecessary downtimes are avoided and that accurate forecasts for completion and follow-up orders are obtained. The digitalized maintenance of machines and tools ensures that maintenance can be better planned and fully documented. This interaction ensures that your machine occupancy planning is always up-to-date and dynamic.
Experience digitalization live
Trade fair season 2024 is here. We will be on site for you at the most important trade fairs and events, giving you the opportunity to experience the digital factory live with the MES Software EMC.
We look forward to welcoming you to our booths.