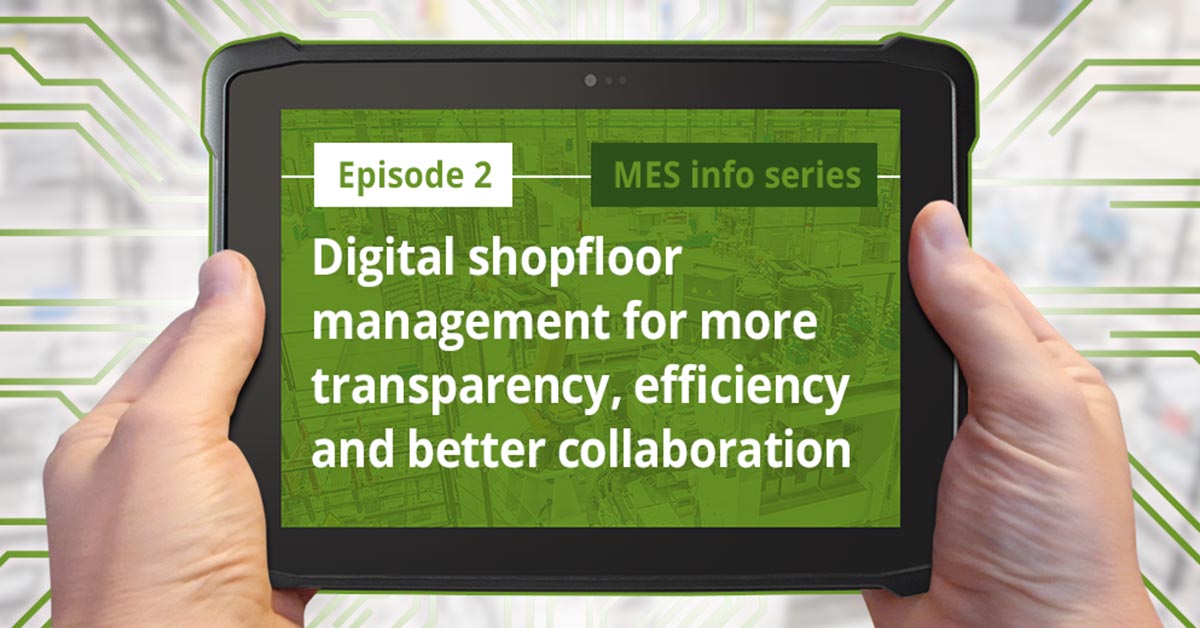
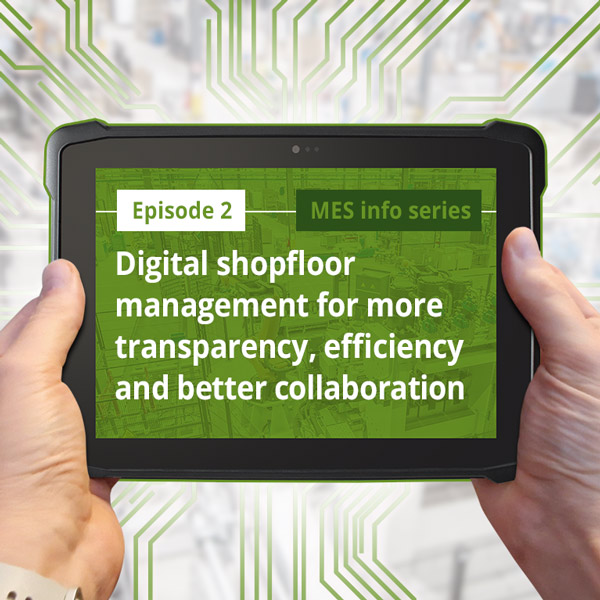
Episode 2 of the MES info series
Every production process is dynamic. And there are countless variables that determine how productive or effective production is. In the digital factory, these variables in the form of real-time information or real-time data are the constant basis for the ongoing progress of production. Data such as utilization rates, OEE, the most common reasons for errors, employee productivity or energy figures are essential for assessing the efficiency of your own production.
Access to and availability of real-time information brings many advantages. On the one hand, the status of current production can be compared with the specifications from order planning and the ERP at any time. Secondly, it actively helps to identify disruptions and deviations in the processes and to take action at an early stage. To make this possible, our MES Software EMC reliably records and bundles all real-time data on the shopfloor and uses it as required – for example as real-time dashboards of ongoing production, in the planning of machine utilization, in analysis or in the creation and distribution of reports.
In this second episode of our MES info series, we will show you how digital shopfloor management can make your production more effective and transparent and thus also ensure better collaboration.
Digital shopfloor management for more transparency,
better collaboration and more efficient processes
Digital shopfloor management for more transparency, better collaboration and more efficient processes
Know, what’s going on
Both the actual value of the current production and the target value of the order are displayed directly on the MES terminal at the machines at all times. The worker can see the current order progress at a glance and can intervene if necessary. Thanks to the rapid intervention, regular operation is restored promptly, resource utilization is increased and deadlines are met.
You can find out how the data from the machines and workstations is recorded in episode 1 of our MES info series.
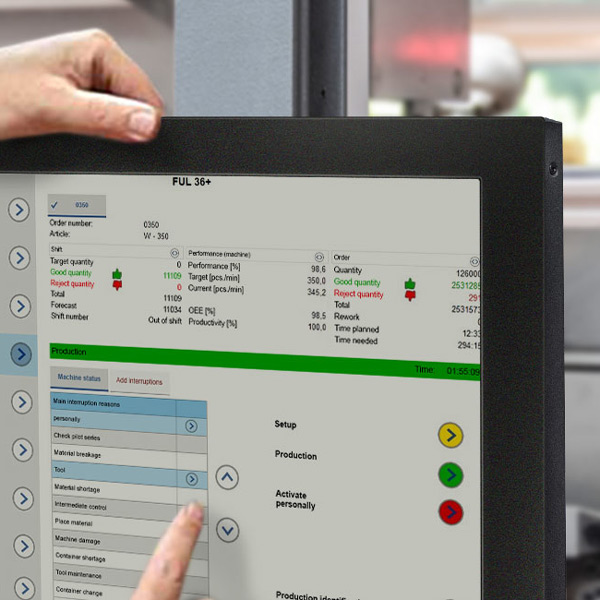
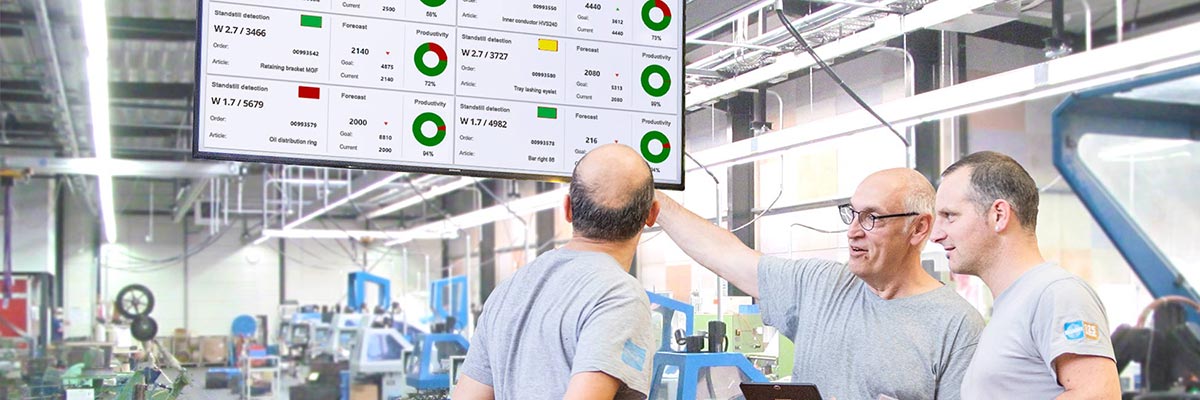
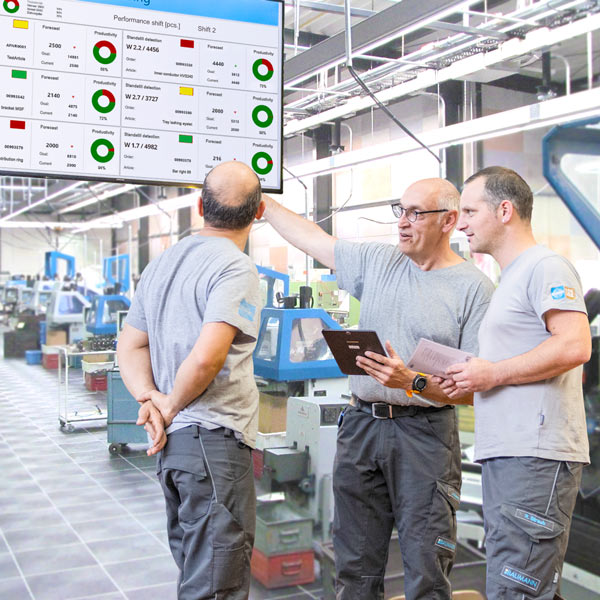
Increasing efficiency begins with recognizing the need for action
Always have a simple and intuitive overview of ongoing production. Meaningful key figures are visualized with the help of individual dashboards both on the desktop and on large screens directly on the shopfloor. This means you always have an overview of the current order progress, key production figures such as OEE or productivity. Directly in your dashboards and in real time.
This allows you to immediately identify machine downtimes, reduced speed, quality losses and system malfunctions. Potential sources of error are visible at an early stage and countermeasures can be initiated promptly.
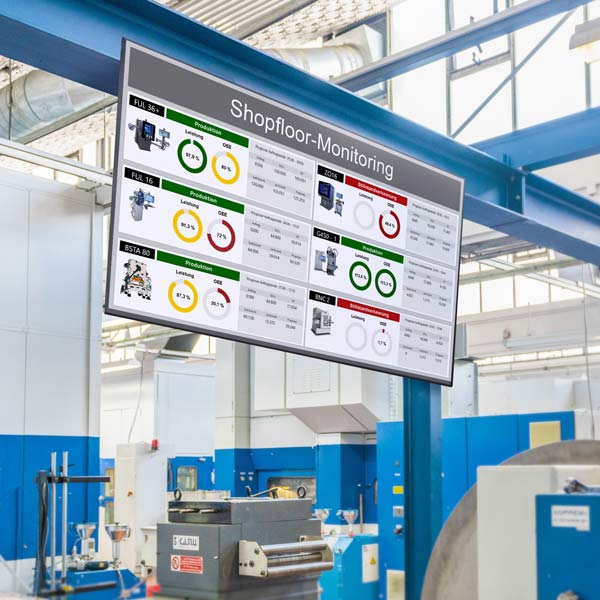
Productivity is driven by structured and systematic action
The visualization of real-time information directly on the shopfloor supports your employees in the structured and targeted implementation of measures. They have an overview of the progress of production at all times.
They can also easily check whether decisions made or measures taken are effective.
This transparent presentation of ongoing production via dashboards sustainably improves collaboration and communication between employees. All with the aim of achieving more more quickly together.
Sustainable optimization of processes through continuous improvement
The real-time information directly from production enables realistic analyses and reports. This not only allows you to compare orders or machines, but also to quickly identify risks and potential through important analyses such as OEE of systems, setup levels, system downtimes, planned/actual time analyses of articles or productivity indicators.
EMC.Reporting enables you to carry out an honest performance analysis and process optimization of production based on sound machine and production data. This enables systematic root cause analyses to be carried out.
With the help of well-founded corrective measures and effectiveness checks, improvements are integrated into your company processes on a sustainable and continuous basis.
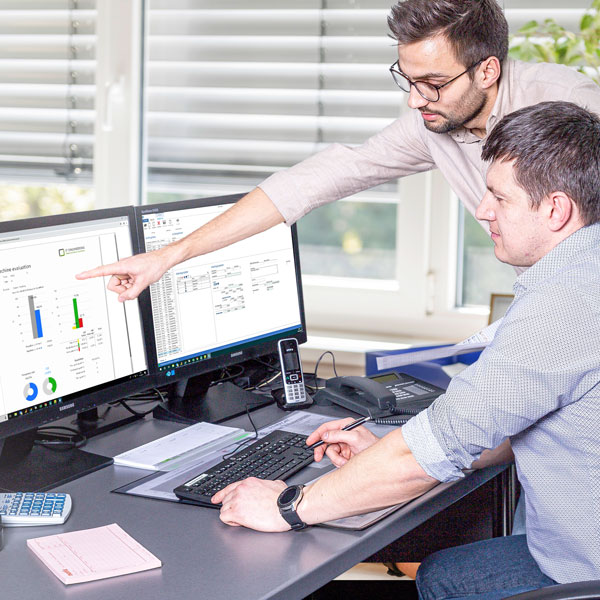
Automated report distribution
A large number of reports can be generated from the real-time data and automatically distributed to the relevant employees or departments.
The systematic execution of analyses and evaluations with the system reports shows cause and effect in process management and controlling. Give your employees the opportunity to analyze their data, gain important insights and make better decisions. This means that success can be measured at any time and in real time.
Conclusion Episode 2
Real-time information is the gold of any production. It enables efficiency and productivity to be actively displayed and evaluated at any time. The real-time production data collected is used precisely where it is useful. This makes working methods easier in the long term.
Thanks to the significantly increased level of transparency regarding ongoing production, you always know where which order is running with which item and with what progress. Delays are immediately visible, problems with material, articles or tools are quickly detected and enable a prompt response.
The knowledge gained from the recorded real-time data is permanently anchored in the system and thus offers the opportunity to gain in-depth analyses of your own production. Important adjustments can thus be found and optimized quickly. With digital shopfloor management, nothing stands in the way of a continuous and sustainable improvement process.