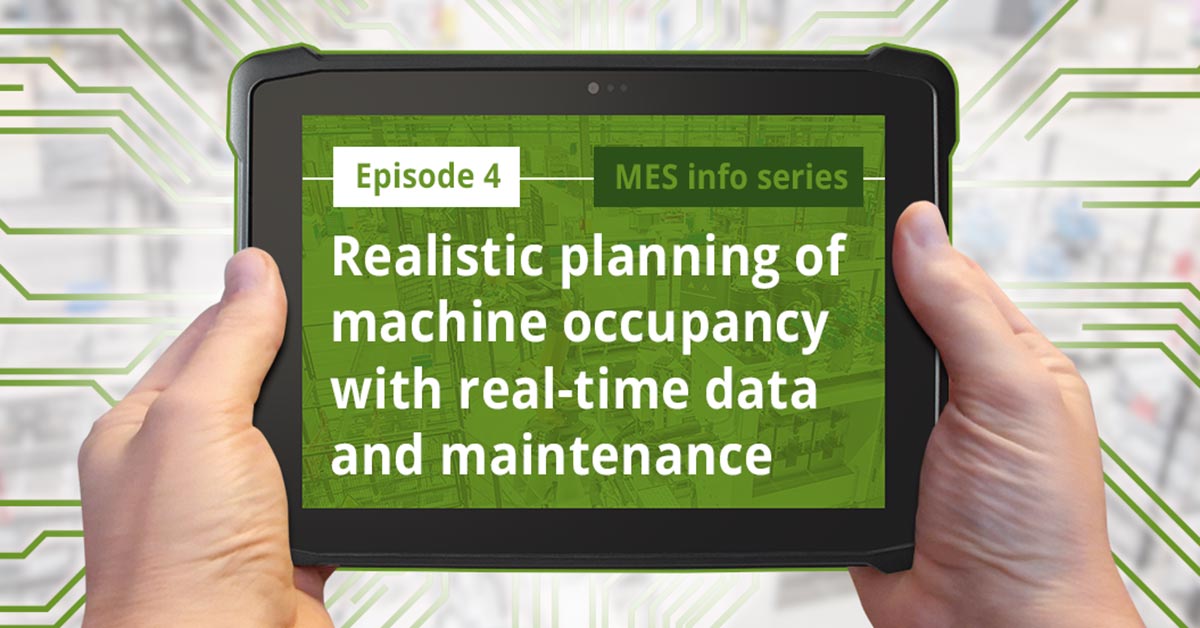
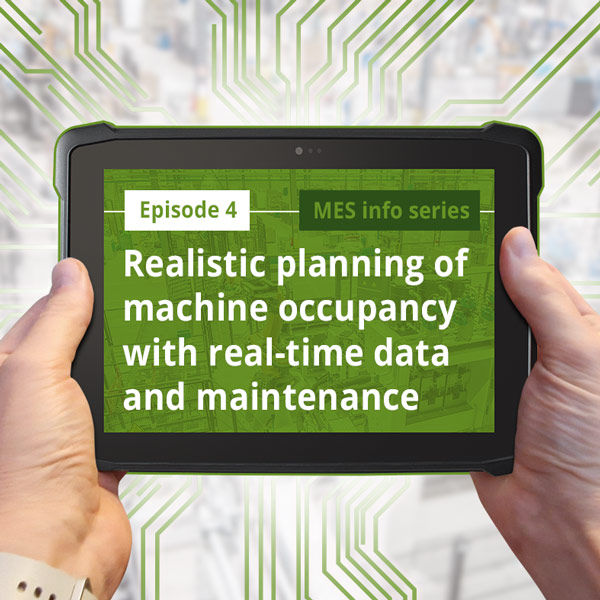
Episode 4 of the MES info series
Proper planning of machine occupancy is immensely important for efficiency and productivity. And one of the biggest challenges in production is keeping the machines running and thus avoiding production delays.
Rough planning with orders from the ERP assumes infinite production capacity. However, what happens live in production, e.g. during a repair or maintenance, does not initially influence this rough planning. In many places, this is done using Excel lists that are laborious to maintain, which have to be corrected daily and constantly reconciled. The effort involved is enormous and the sources of error are high.
This is not the case in the digital factory. Thanks to the direct connection to the machines, the detailed planning of machine allocation always takes into account real-time data directly from production. This means that if the machine stops, for example if a tool breaks, the planning automatically adapts and reliably reschedules follow-up orders. Predefined maintenance and repairs are also taken into account and scheduled correctly.
In the fourth episode on the topic of digitalization, we will show you how you can achieve realistic, resource-optimized planning of machine occupancy using real-time data and the integration of maintenance and repairs.
Realistic planning of machine occupancy
with real-time data and maintenance
Realistic planning of machine occupancy with real-time data and maintenance
Machine occupancy planning with direct connection to the machine
Realistic production planning for machine utilization is the be-all and end-all. This is made possible by the direct connection to the machines. The roughly planned orders are received by the ERP and supplemented and adjusted in short-term planning with the data collected in real time on the shopfloor (machine occupancy, tool allocation, employees or downtime reasons). The work processes for the orders are then planned for the individual resources (machines, workstations).
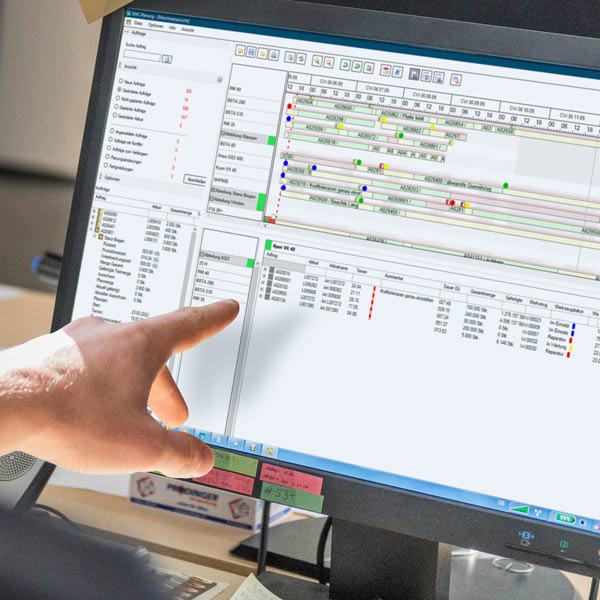
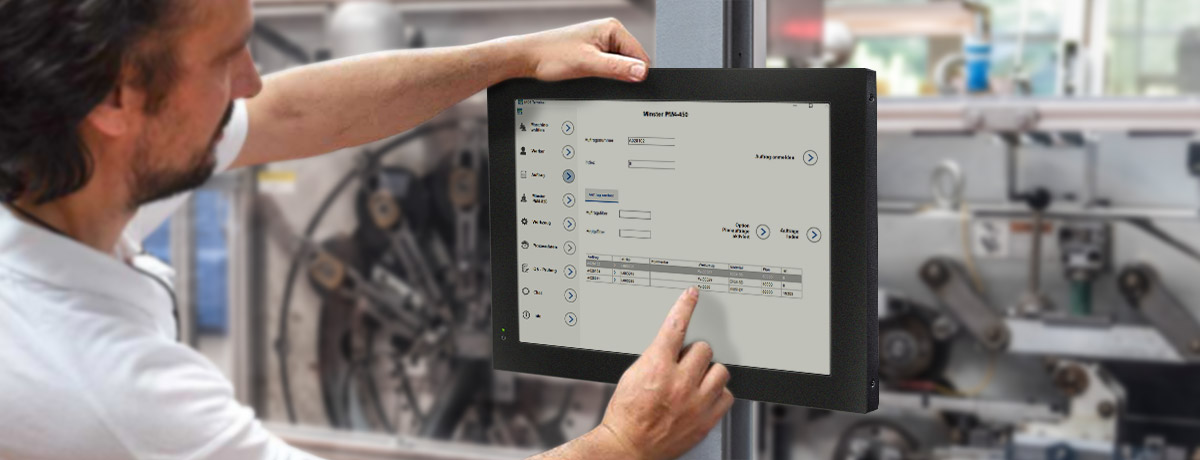
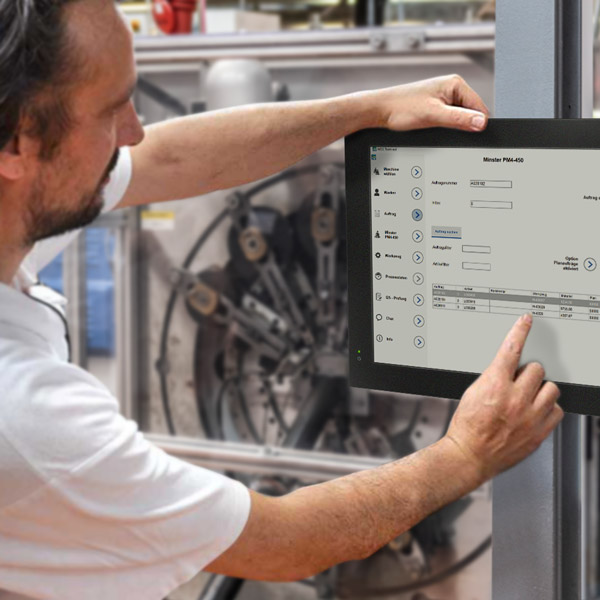
Bye-bye printed planning lists
Planning in digital production makes printed production lists and their distribution in production superfluous. This means that the current plan sequence is displayed directly on the MES terminal and in the shopfloor dashboard. In addition, the order is registered directly via the displayed planning list.
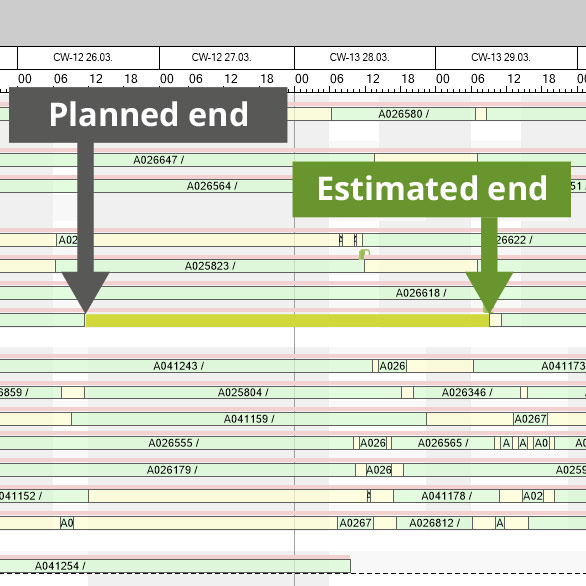
Get to your goal smarter with the navigation function
The navigation function automatically adapts your planning to the current order progress of the machine and visualizes the planned order sequence digitally on the machines.
The actual progress is continuously reported back to the planning after the start of the order on the machine – in real time. The planning is then updated automatically, carries out a forecast calculation for the end of the order and updates the start date of the following orders.
In addition, predefined machine or tool maintenance is automatically taken into account in the machine document planning and the planning is adjusted accordingly.
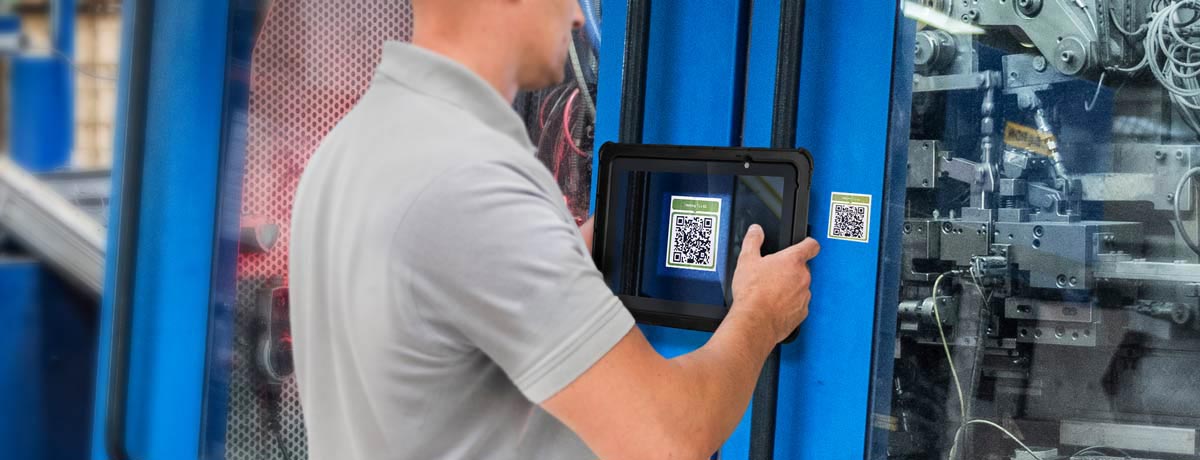
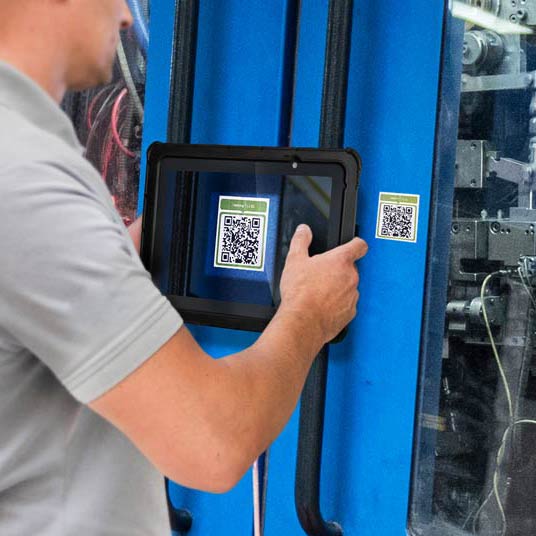
Keeping the machines in optimum condition
It goes without saying that machines need to be regularly serviced, checked and maintained. This has a lasting effect on the quality of your own production and ensures that the machines run smoothly. The EMC.maintenance module makes it easy to neatly file and document important machine maintenance.
Instructions, maintenance steps or special maintenance procedures can be stored for each machine and peripheral equipment – both automatically and manually. In addition to the individual maintenance steps to be carried out, maintenance cycles (daily, weekly, monthly, annually, etc.) can also be defined individually. Typical checks or maintenance tasks, such as a grease change on the gearbox, are also created as maintenance tasks and can therefore be easily carried out and documented as required.
The system continuously checks the status of the machines and reports upcoming maintenance. If maintenance is due, it can be started simply by scanning a QR code attached to the machine, for example.
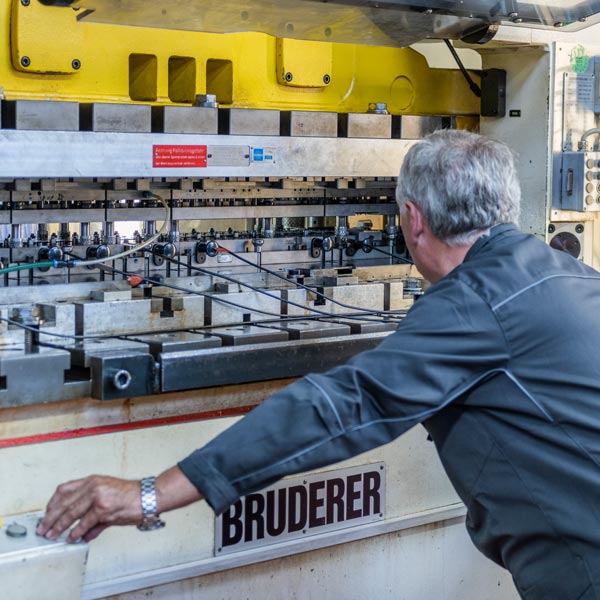
Digitized tool maintenance
With the EMC maintenance module, you can carry out maintenance, repairs and servicing, including all components and spare parts used, both manually and according to individually predefined maintenance cycles. This enables high technical availability and reliable maintenance.
More efficient production and planning with the integration of tool maintenance
The digital information exchange and access provided by the MES Software EMC enables predictive control of individual production processes. For example, in the event of a repair, the toolmaking department is informed directly from the machine terminal. This information is also sent directly to production planning without any detours.
This means that the planner knows the current tool status at all times. Upcoming maintenance and current repairs are automatically integrated into detailed planning. This ensures realistic and smooth production processes. In addition, the tool shop receives information from planning about which tool is needed when and what maintenance is due.
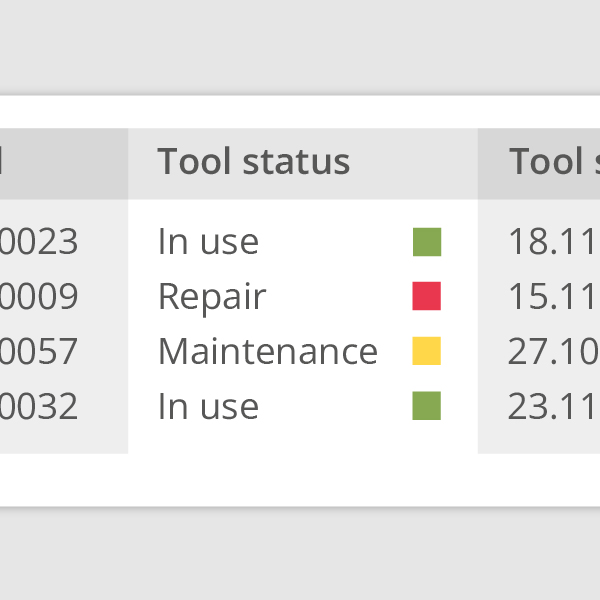
Digital maintenance management
The documentation of maintenance and repairs is complete and comprehensive. All machine maintenance, tool maintenance and repairs are documented in the digital life cycle card of the MES Software EMC. The current status, availability and history of the tools are also stored in the digital tool card.
Further information such as articles and orders are linked. Installed spare parts and their number can be traced exactly.
The complete workflow for digital maintenance management can be called up digitally at any time, directly at the machine terminal or via mobile tablets. Maintenance can be easily started either manually via the portal of the MES Software EMC or by scanning a QR code attached to the machine or tool.
Intelligent analysis
Which tool inserts are responsible for production downtimes? Which spare part is replaced most frequently? How many benders are kept in stock for a production run?
Thanks to the complete, digital recording of inserts or spare parts, for example, the tool design department can access a lot of data to optimize the tool. This makes a significant contribution to increasing productivity and effectively avoiding machine downtime due to unplanned maintenance.
Conclusion Episode 4
There will always be delays in production and they are difficult to avoid. How these are dealt with and what measures are taken to reduce them makes a decisive difference to how well planning works and therefore how productive and efficient production is.
Resource-optimized planning with the integration of real-time data from production and properly scheduled maintenance ensures that unnecessary downtimes are avoided and that accurate forecasts for completion and follow-up orders are obtained. The digitalized maintenance of machines and tools ensures that maintenance can be better planned and fully documented. This interaction ensures that your machine occupancy planning is always up-to-date and dynamic.